PICKLING AND PASSIVATING
Pickling and passivating is an effective surface treatment to clean stainless steel sheet metal and to restore and strengthen its corrosion resistance.
Because Contour has its own in-house pickling and passivating installation, we are able to work cost-effectively and remain flexible in our planning. We have full control over the priorities in our pickling line, and we are not dependent on time-consuming transport to an external company.
In this article, we discuss the benefits, process, and application of pickling and passivating.
WHAT IS PICKLING AND PASSIVATING?
Stainless steel (RVS) is resistant to rust thanks to a chromium-rich oxide layer that forms naturally on the surface of the material.
When the surface of the material becomes damaged, the protective oxide layer is broken. In reaction with oxygen from the atmosphere, this oxide layer will naturally restore itself.
When the stainless steel surface is contaminated, for example by a welding process, the oxide layer locally contains a lower chromium content. The oxide layer cannot always recover on its own. This makes the material vulnerable to corrosion.
The process of pickling and passivating solves this issue. During pickling, a thin layer of metal, including the oxide layer and contaminants, is removed. During passivating, the oxide layer is restored in a controlled process. The result is a consistently pure oxide layer that offers good corrosion protection and also looks aesthetically pleasing.
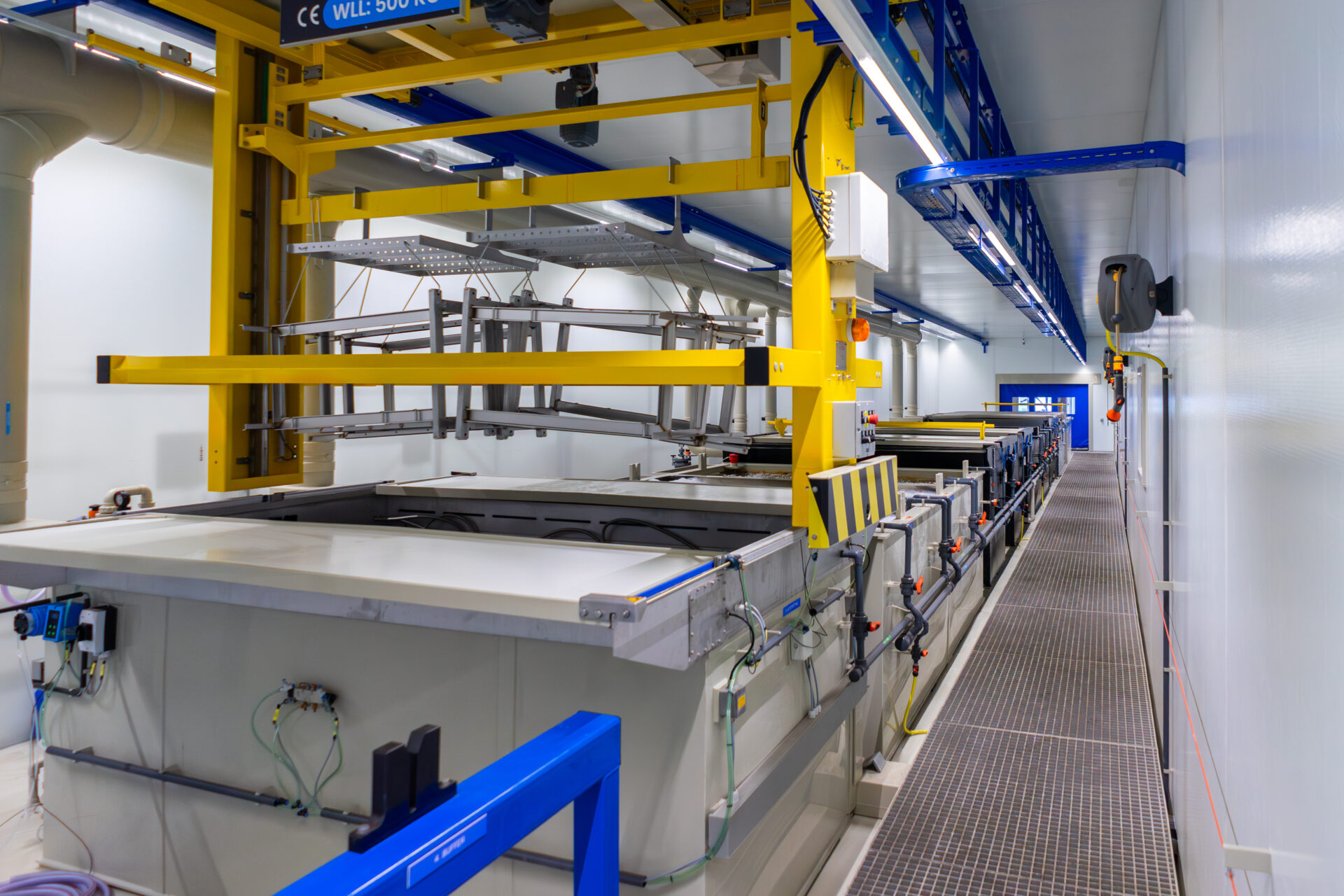
PICKLING INSTALLATION
PICKLING & PASSIVATING
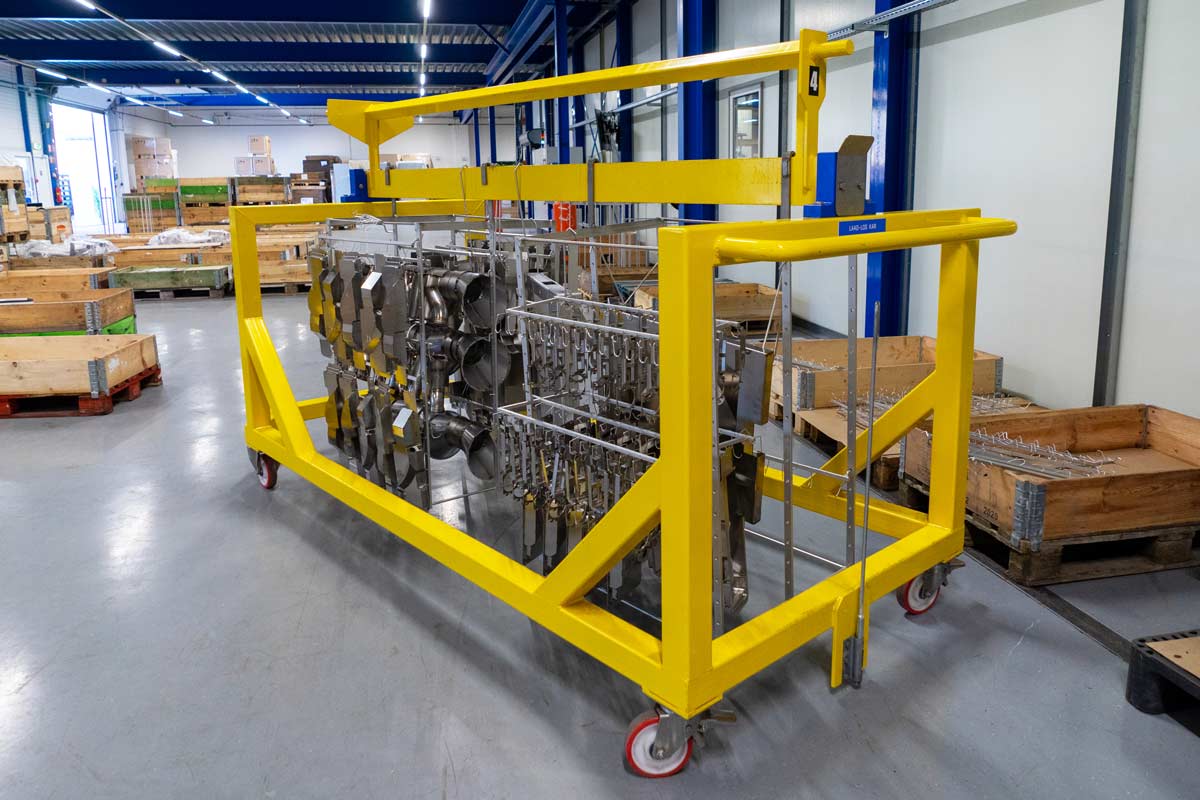
PICKLING TRAVERSE
PICKLING & PASSIVATING
PICKLING
The pickling process focuses on removing contaminants and oxidation from the surface of stainless steel (RVS). A pickling fluid is used that chemically reacts with the oxide skin on the stainless steel surface.
Pickling can be carried out with a pickling fluid that can be applied in different ways depending on the size and structure of the object to be treated. This can range from immersing in the pickling fluid to applying a pickling paste or spraying with spray pickle. The most suitable method depends on the product being treated and its size. At Contour, we work with immersion pickling. Virtually all products we produce fit into the pickling bath.
The fluid reacts chemically with the oxide skin on the stainless steel surface, resulting in a metallically clean surface.
After pickling, the stainless steel surface is rinsed to remove the pickling fluid and prepare the surface for the passivating process.
The pickling fluid is usually composed of nitric acid and hydrofluoric acid, diluted sulfuric acid, hydrochloric acid, or iron sulfate. Nitric acid effectively removes iron-based contaminants, while hydrofluoric acid dissolves oxide layers on the stainless steel surface. These acids can be combined in various proportions.
During the pickling process, the pickling fluid is applied to the surface of the stainless steel. Here, the acid reacts with the oxide skin on the stainless steel, resulting in the formation of hydrogen gas and a dissolved oxide. Hydrogen gas helps remove the oxide skin from the stainless steel surface, creating a clean, metallic finish.
In addition to cleaning the surface, slight surface damage such as roughness, scratches, pits, and stains can also be removed by the acid. The pickling process thus yields a smoother and cleaner surface.
It is important to thoroughly rinse the stainless steel surface after the pickling process. This ensures that any residues of the pickling fluid and other contaminants are completely removed from the surface.
PASSIVATING
Passivating stainless steel (RVS) focuses on improving corrosion resistance of the metal by forming an oxide layer on the stainless steel surface. This oxide layer is rich in chromium and creates a protective barrier that improves the corrosion resistance of the metal.
This process can be carried out by immersing the stainless steel in an oxidizing bath, such as nitric acid or sodium dichromate. The acid causes a chemical reaction with the stainless steel surface, resulting in the formation of an oxide layer on the metal surface.
The formed oxide layer is very thin and evenly distributed over the stainless steel surface. This protective layer restores the corrosion resistance of the stainless steel and better withstands further corrosion attacks than an unprotected surface.
The acid bath is followed by a thorough rinsing to remove any remaining acid.
A properly executed passivating process can significantly improve the lifespan and appearance of stainless steel.
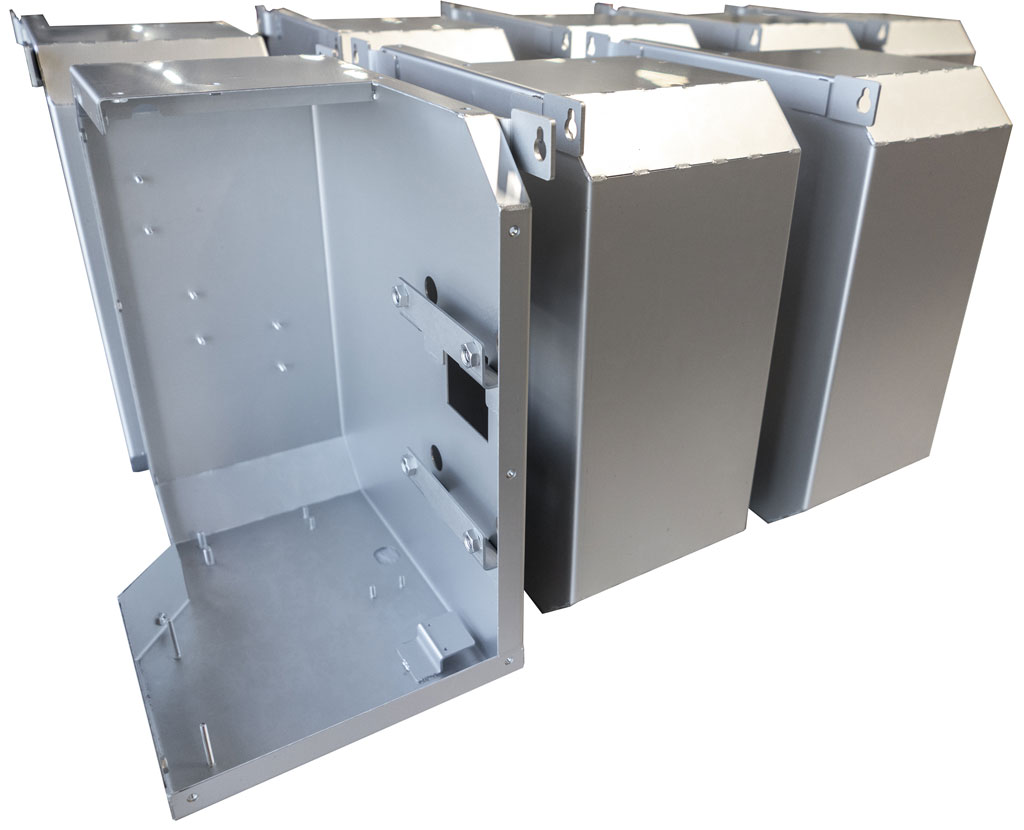
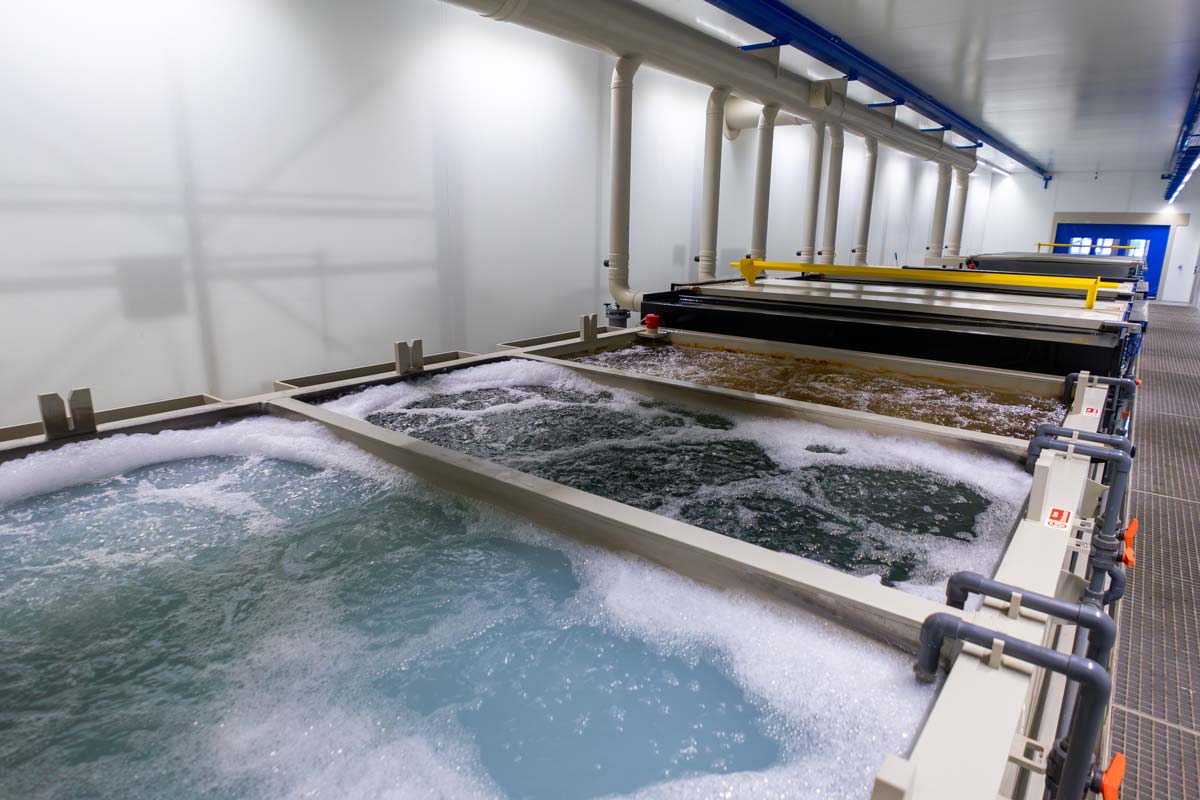
RINSING BATHS
PICKLING & PASSIVATING

PICKLING INSTALLATION
PICKLING & PASSIVATING
PEOPLE AND ENVIRONMENT
Our pickling installation is set up in a way that is responsible for both people and the environment.
The installation is fully enclosed with its own extraction system. A fully automated overhead crane moves the pickling traverses between the baths.
The entire installation is placed in a fully welded plastic basin, which prevents fluids from leaking into the environment.
The chemicals used are also chosen to minimize impact on people and the environment.
DIFFERENCE BETWEEN PICKLING AND PASSIVATING
The difference between pickling and passivating is that pickling is focused on removing both the existing oxide layer and any contamination from a stainless steel surface, while passivating is focused on subsequently restoring (reapplying) the oxide layer.
In other words, pickling is the cleaning step prior to passivation.
It is the oxide layer that makes stainless steel resistant to rust. Any contamination of the oxide layer reduces the corrosion resistance. The pickling and passivating process restores the protective oxide layer in a controlled manner.