COMPANY HISTORY
Explanation
This page shows archive images of Contour in Winterswijk. Do you have comments or additions? Do you have any (visual) material that is still missing here? Or are there any inaccuracies on this page? Then please let us know via info@contour.eu
Contour was created from a merger of the companies "Sorba Precisieplaatwerk," "Thavo," and "Lenting." That is why you see the names and logos of these companies returning on this page. Unfortunately, we do not have any historical visual material available in our archive for the Thavo and Lenting companies.
We want to thank the (former) colleagues who have contributed since this page was published! It is wonderful to experience how involved many of the former colleagues still feel, and how they often look back positively on their past at the various companies from which Contour originated.
Table of contents
The 1950s & 1960s
Employment in Winterswijk
This image shows the original company building of Sorba Precisieplaatwerk on the Industrieweg in Winterswijk in the 1960s.
The building in this photo is still used as a storage location in 2022, but it will likely be demolished in 2023.
The company name Sorba came from the names of the company's founders, Messrs. van Sorgen and Bax.
Sorba was originally founded in Gouda. The company later moved to Winterswijk. The distance to the German customers was thus smaller. In addition, due to the end of large-scale textile industry in Winterswijk, there was a shortage of employment. By moving, Sorba could help address that. At the time, the municipality made it possible for the company to obtain a loan to finance the move.
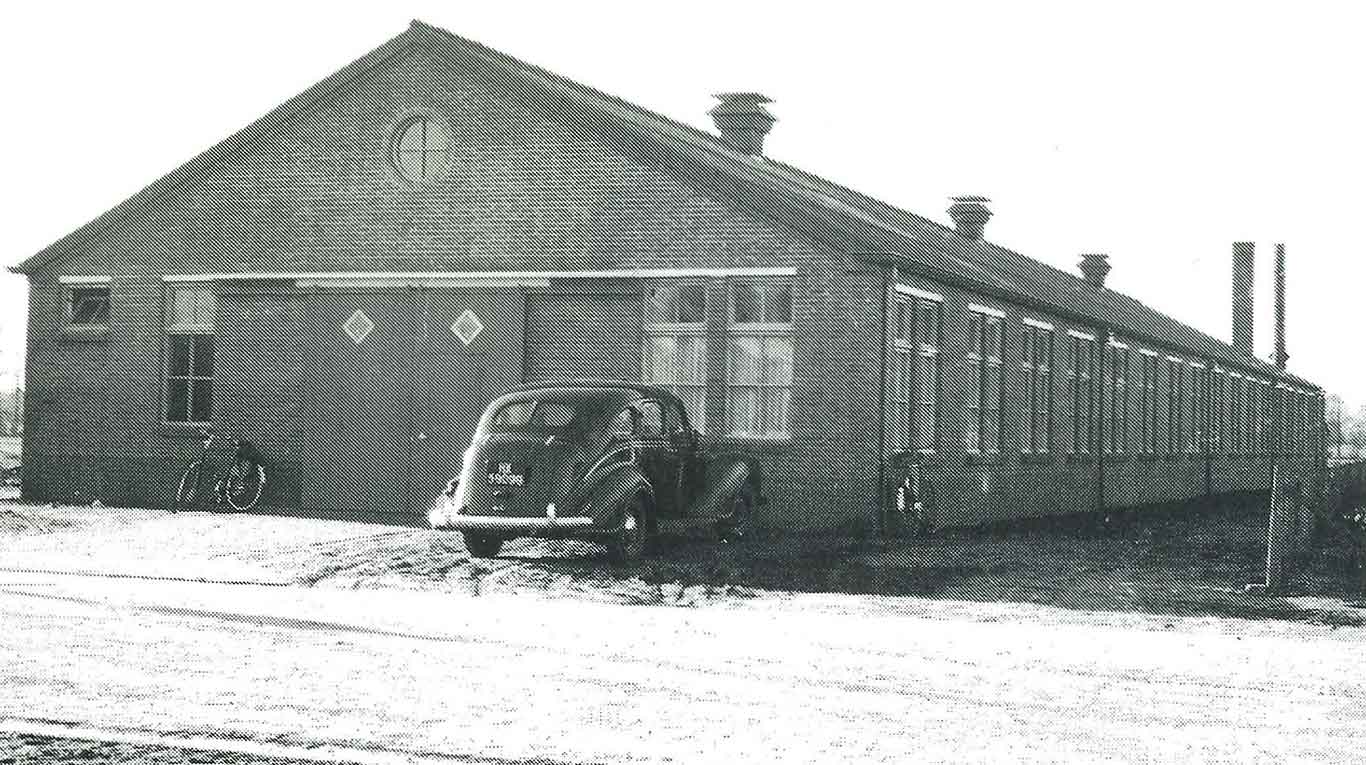
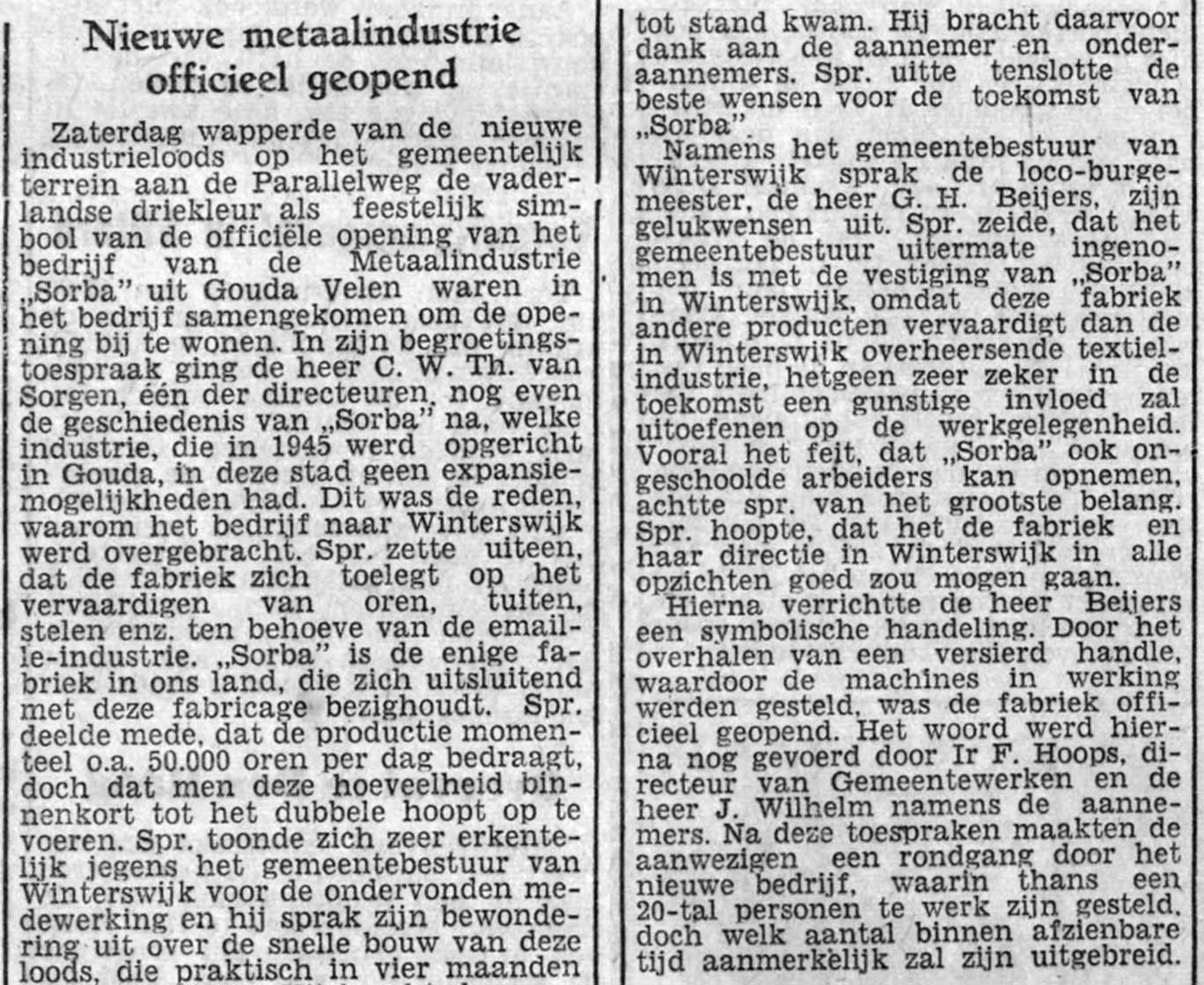
03 Dec 1951 – Twentsch Dagblad Tubantia
Drive system with belts
This is one of the oldest photos in our archive. On the right, you can see machines that were still driven by a central drive system instead of electricity.
The machines are connected to this drive system with belts. In the background, you can see the sliding doors from the above photo.
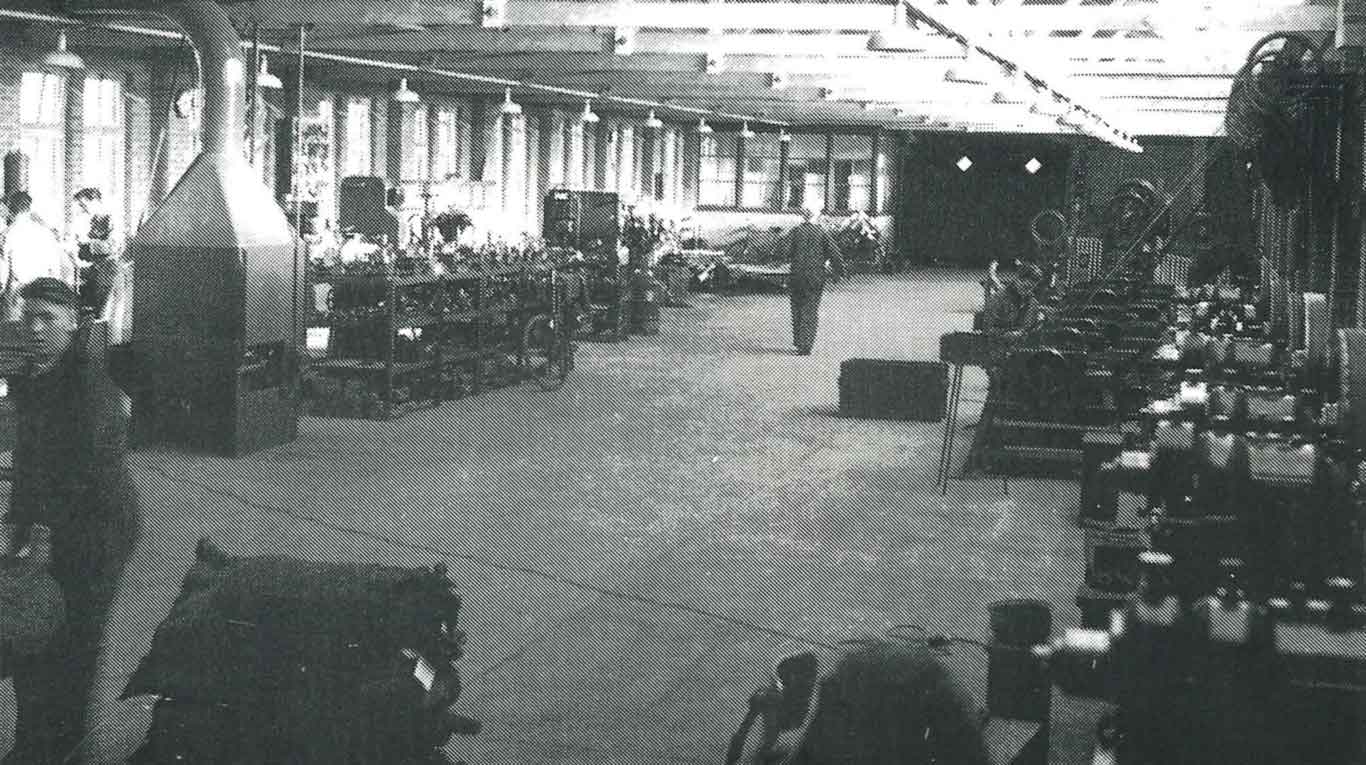
Electrification advances
The electrification of production machines is on the rise. In this photo, you can see a setup of electrically driven eccentric presses with which sheet metal was pressed and punched. They are the distant predecessors of the punching machines and press brakes we use today for sheet metal processing.
Fluorescent lighting also makes its appearance in this photo. In the background, you can still see the older type of lamps hanging.
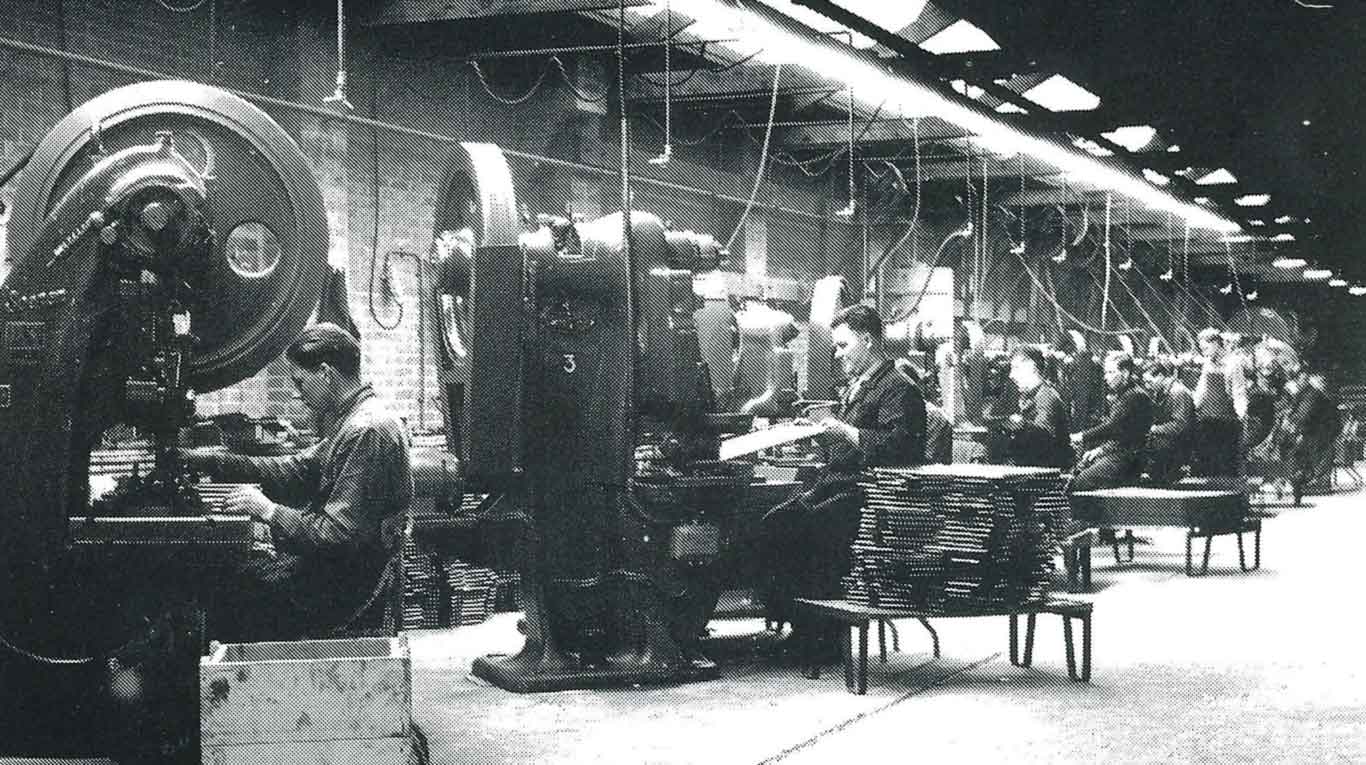
Product: The Sorba oven
The company once had a line of consumer products. In this photo, a Sorba gas oven as produced in the 1960s.
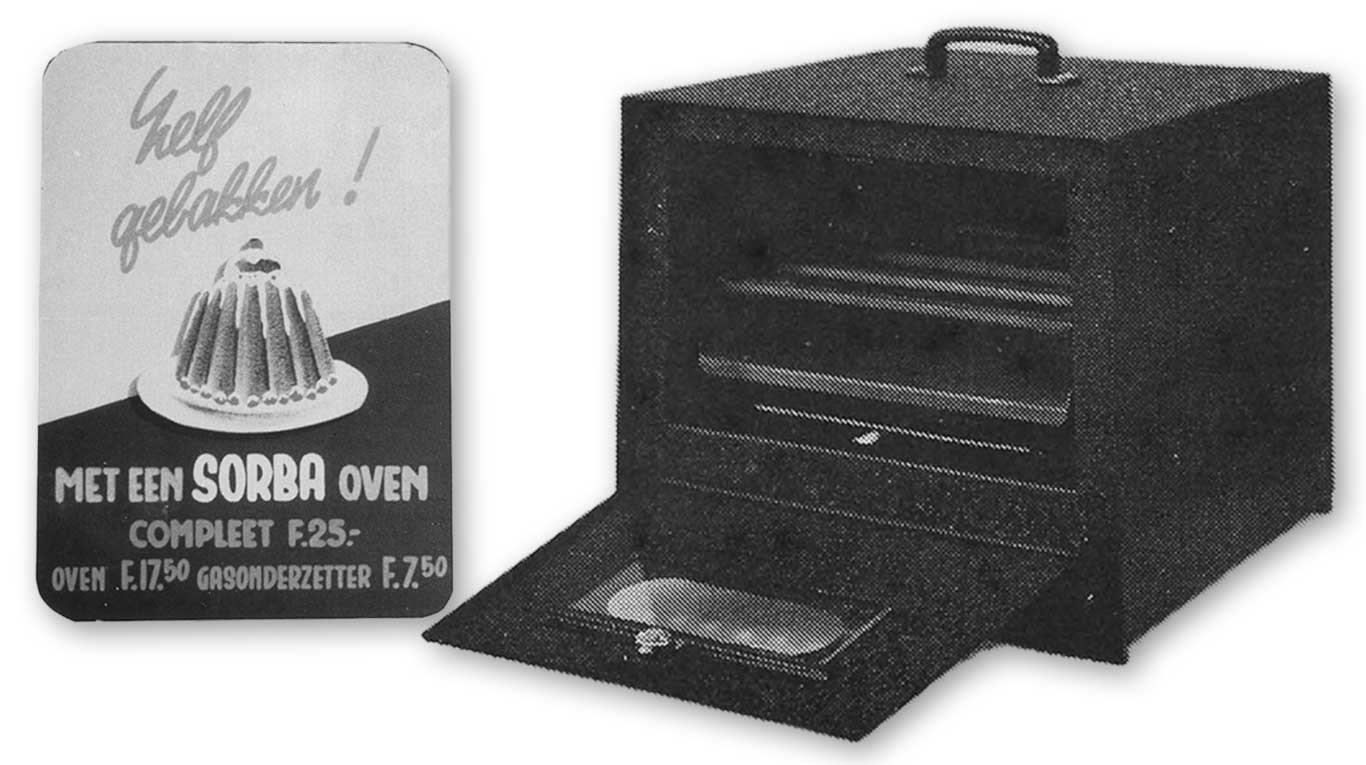
Factory hall photo
You now see the eccentric presses from the previous photo on the left in the picture. In the front on the right, you see a compressor. Behind it, an electric hardening furnace. In the back on the right, there are several electrically driven hydraulic presses.
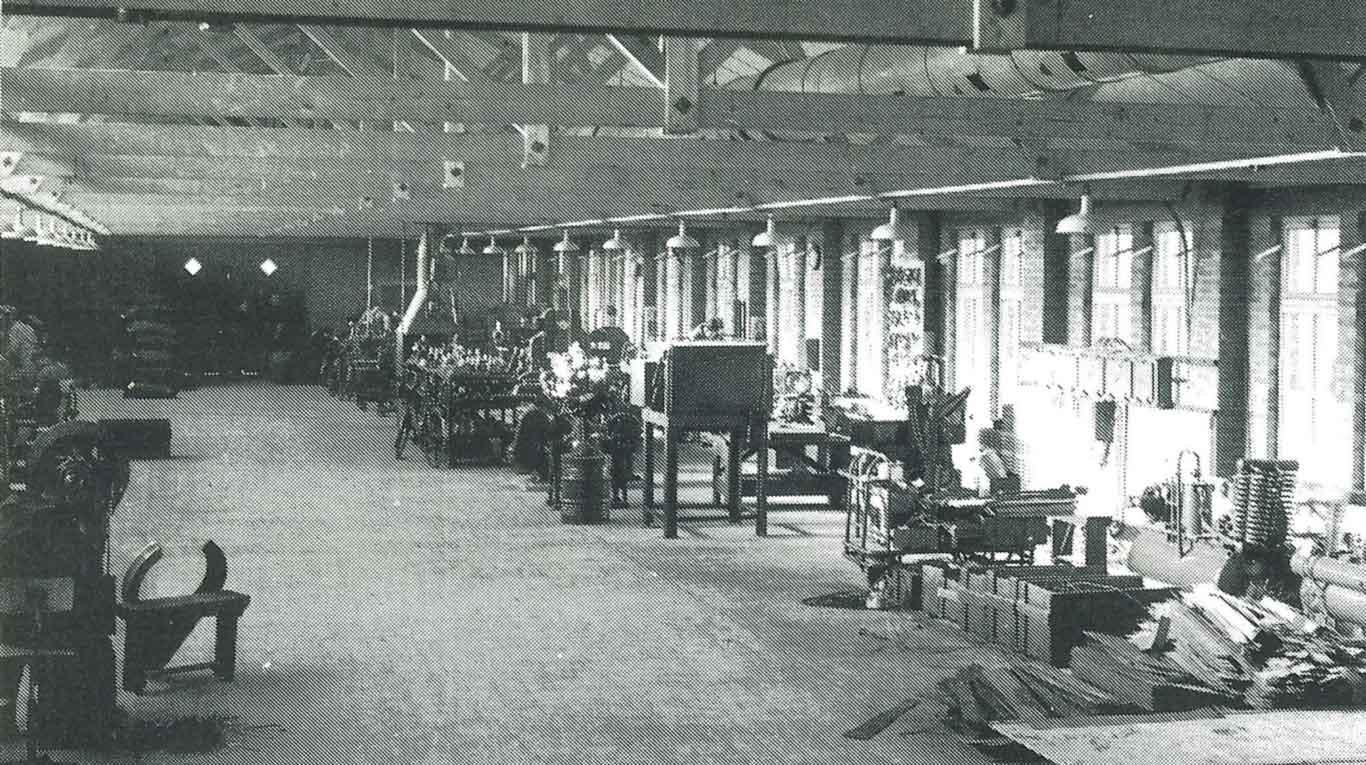
Guillotine shears
In this image, you see our former colleagues operating a guillotine shear used for cutting sheet metal to size.
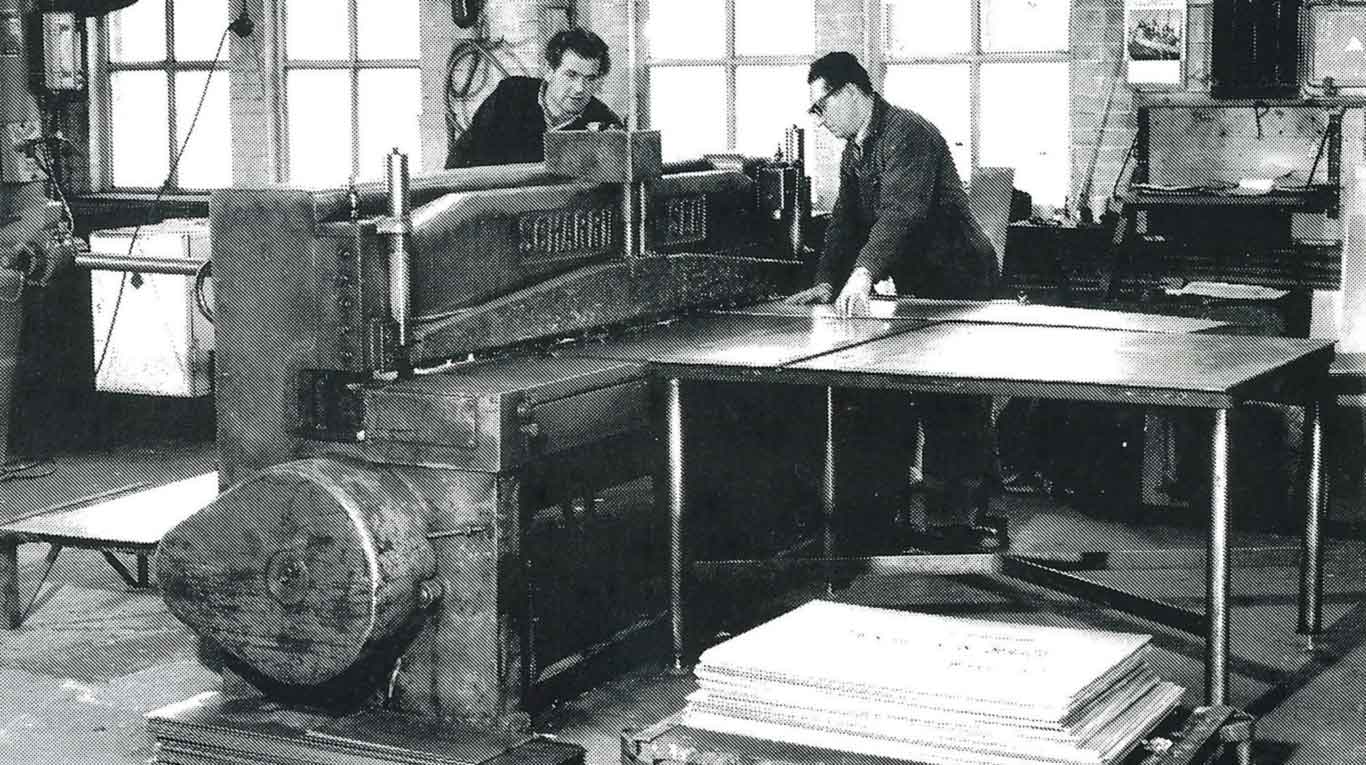
Product: Watering cans
Another example of one of the products produced in the 1960s: watering cans.
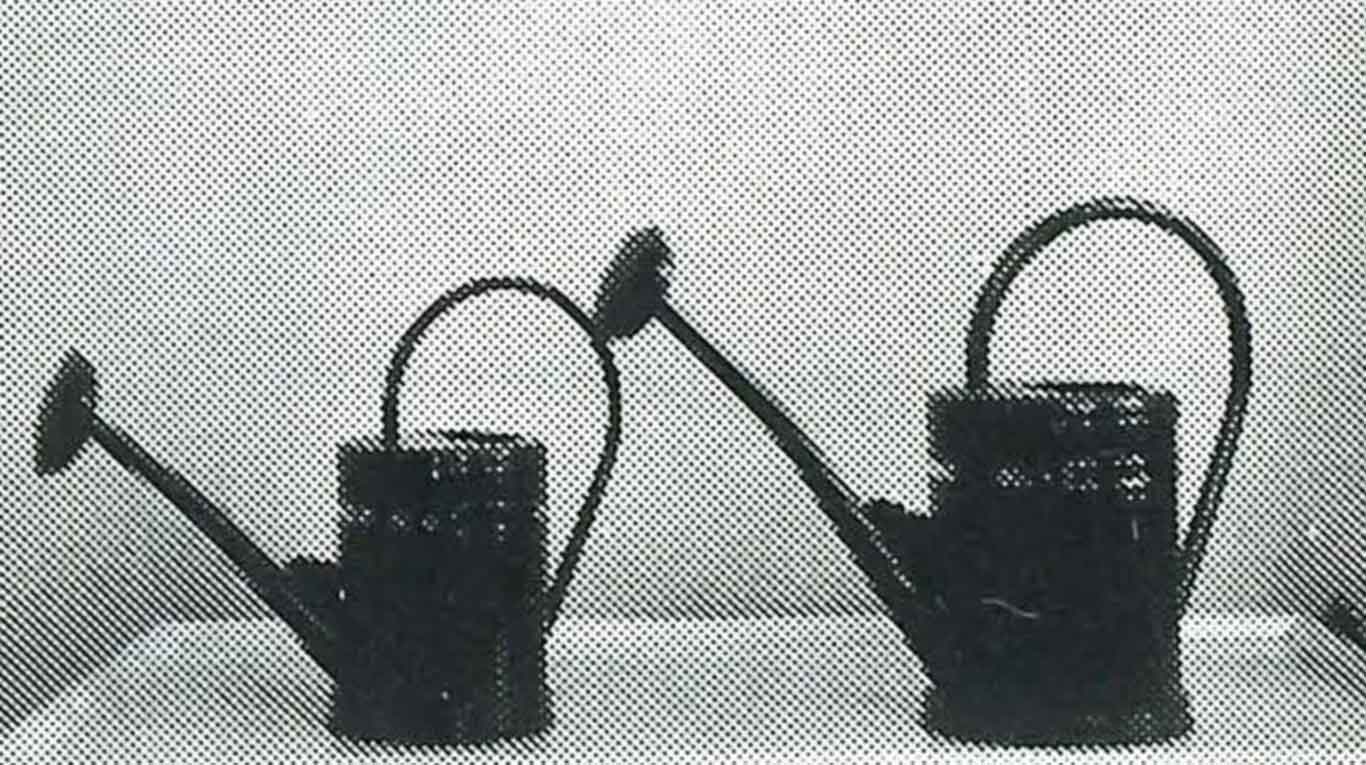
The 1970s
Aerial photo
This aerial photo was taken in the 1970s. We see that the company has grown significantly in size compared to the earlier photos.
The original building from the first photos can be seen at the front on the right, directly behind the newly built office with a flat roof.
The production area has expanded considerably with various halls that have been added on.
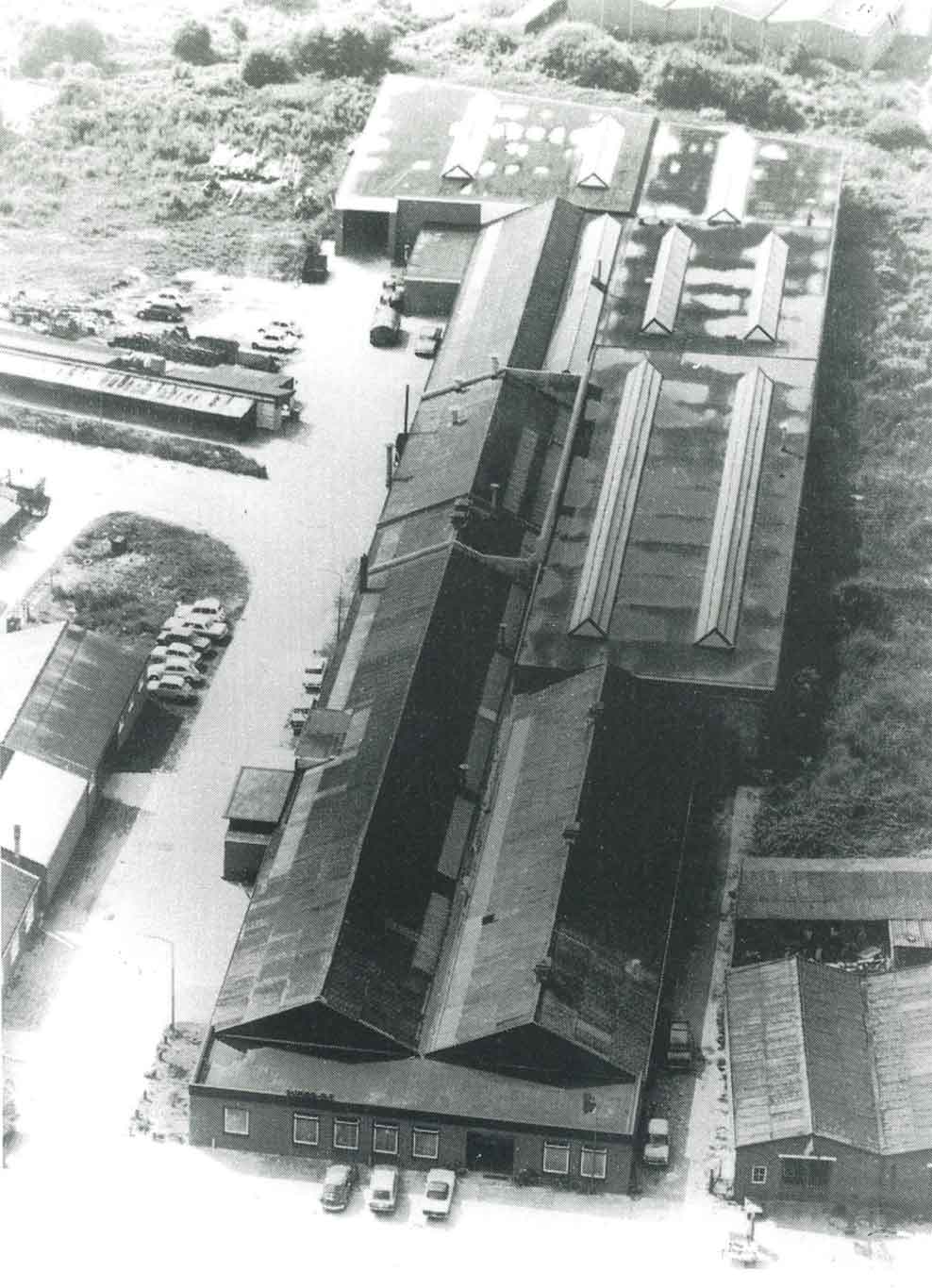
Machining metal
Still in the same building as in the earlier photos (recognizable by the characteristic window frames and roof construction), you see here a setup of electric lathes (right), a column drilling machine (left in the back), and a surface grinder (left in the front).
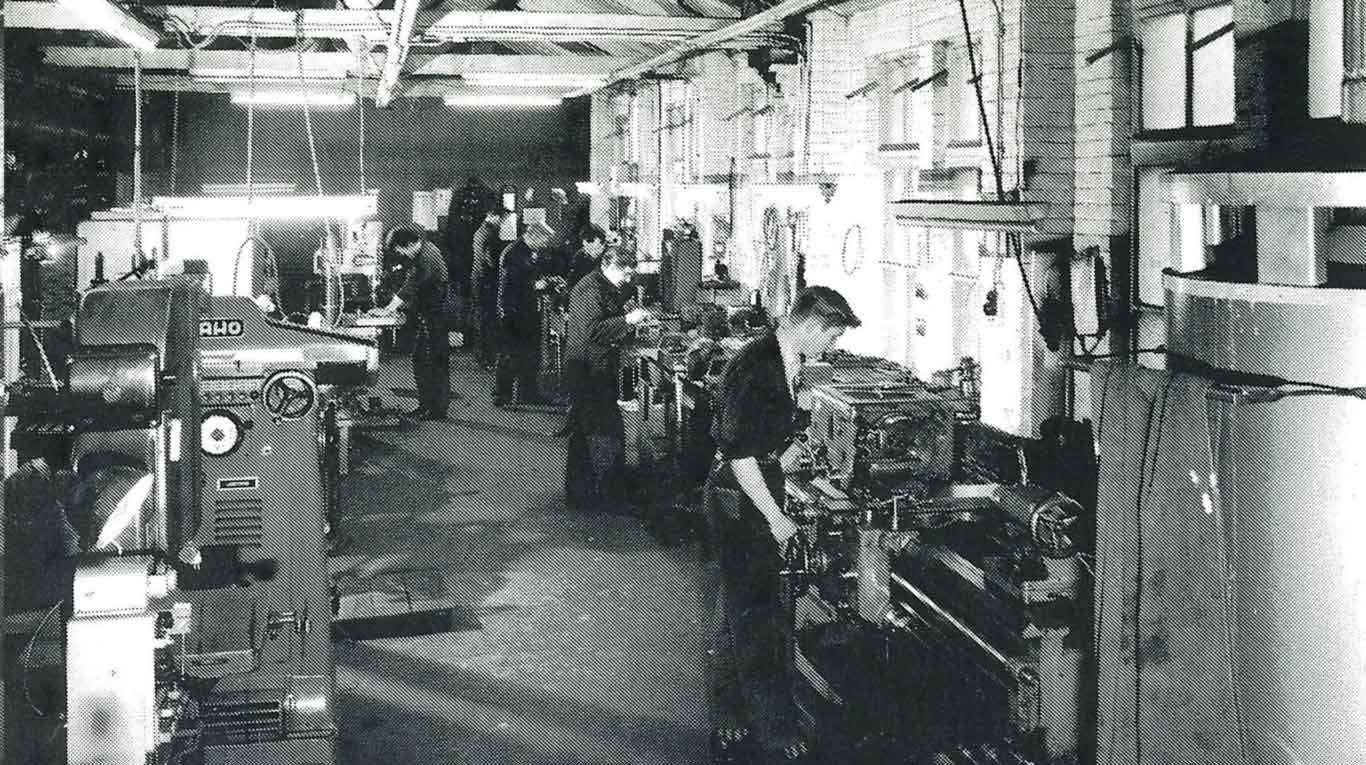
Wet painting
Metal products are being given a coating here. The already sprayed products hang on the left in a drying rack. The process of wet painting was later replaced by a powder coating installation. We now outsource wet painting to companies specializing in it.
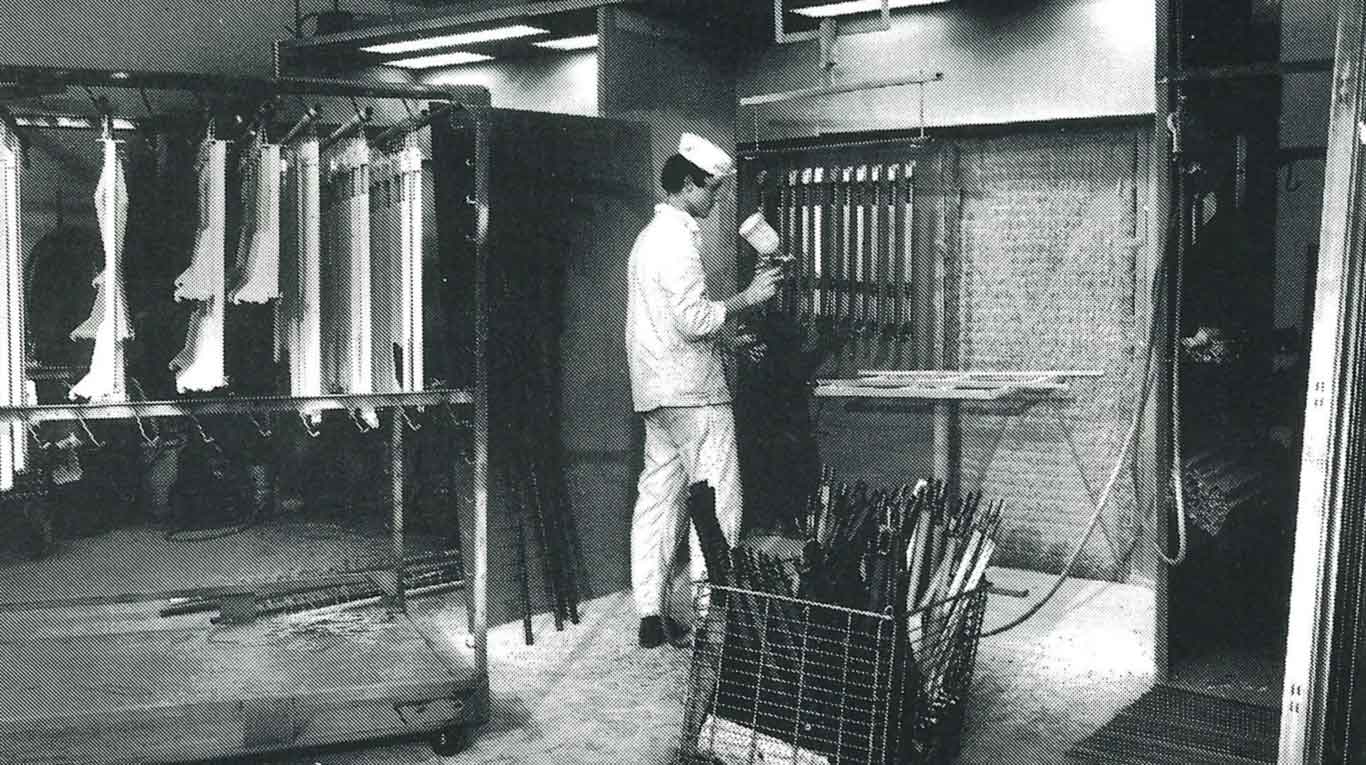
Products in view
In this photo, we see various sheet metal products that were made in the 1970s.
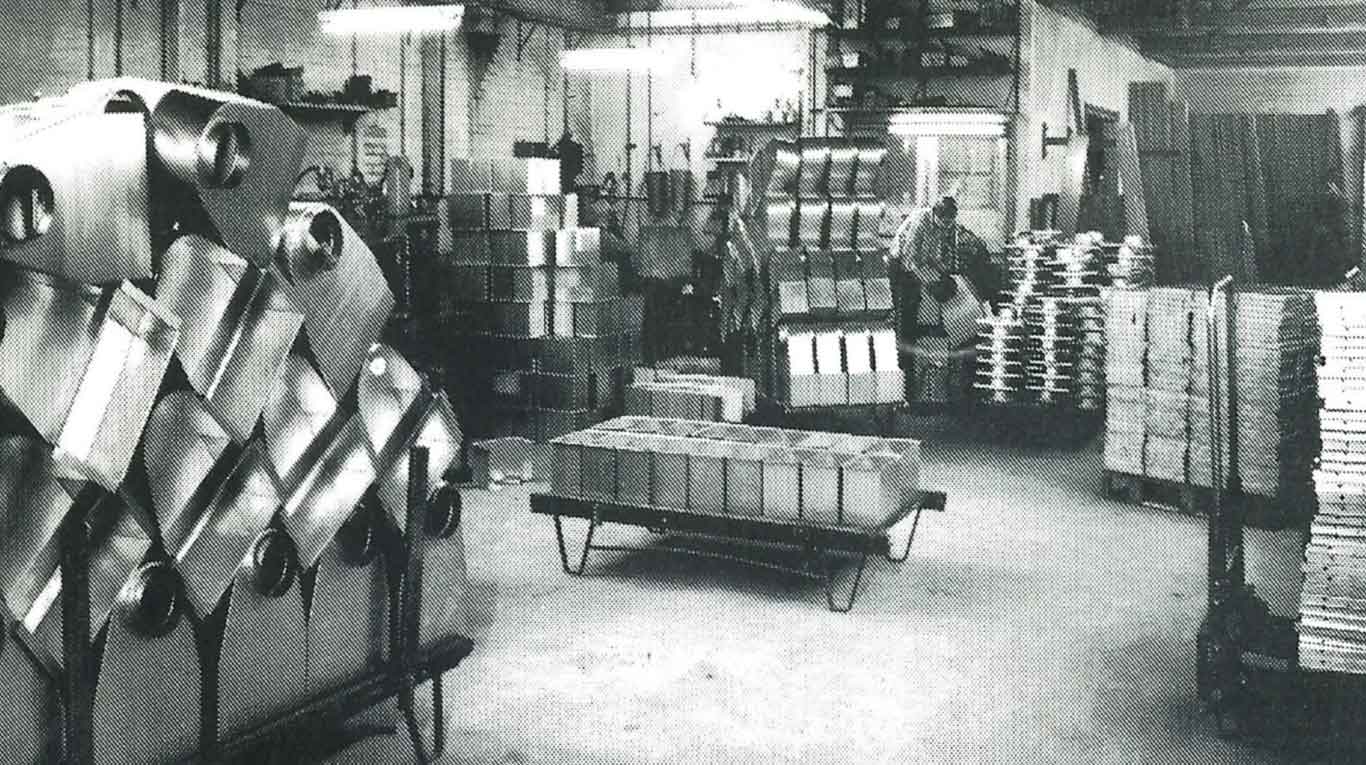
Gas welding
We can rightly claim decades of experience with thin sheet metal as well. This photo shows a sheet metal part being welded. As with TIG welding, material is manually added to the weld pool.
We no longer use the gas welding process nowadays. We now produce our welded assemblies using the latest techniques such as TPS/i, CMT, TIG, and MIG/MAG welding.
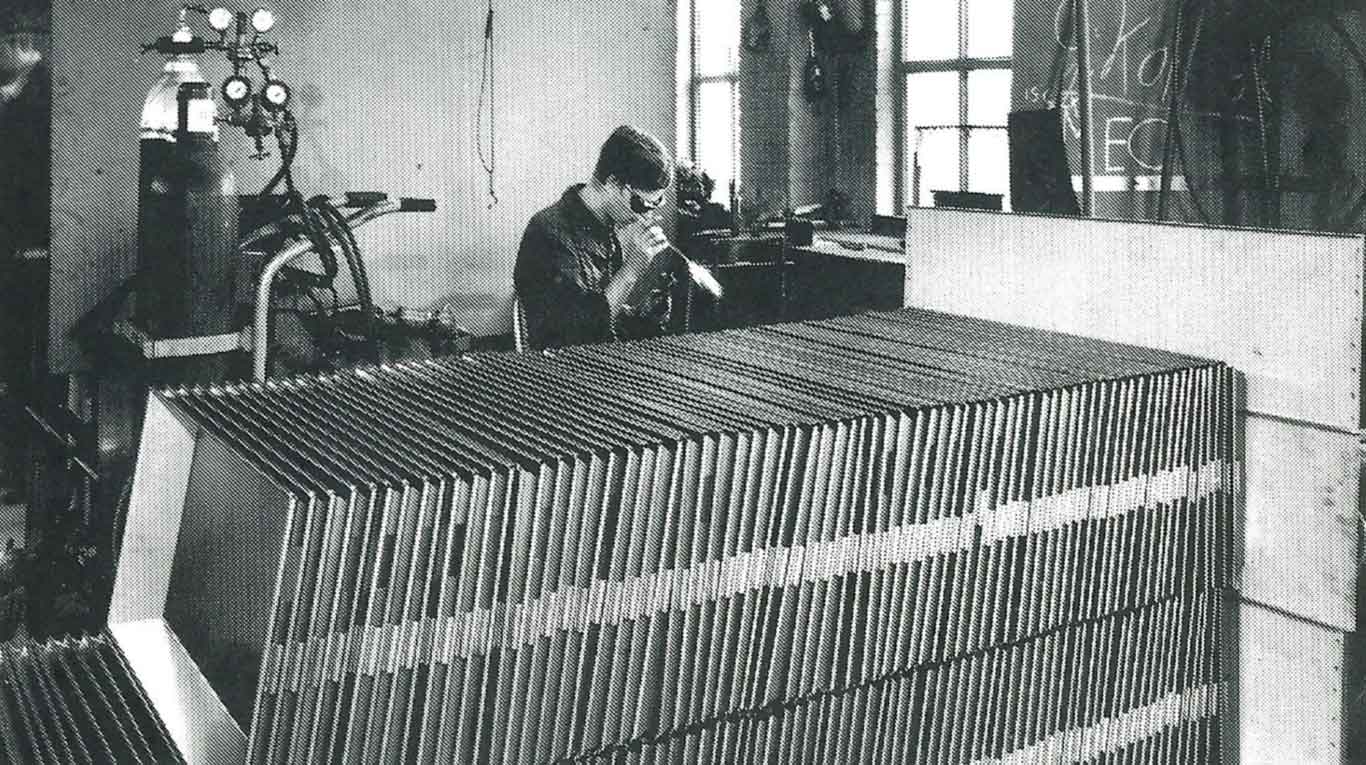
Metal strip punching line
The CNC punch and laser cutting machines we use today for sheet metal processing did not exist yet back then. An alternative was punching blanks from a metal strip. The metal was fed from a coil to the punching machines.
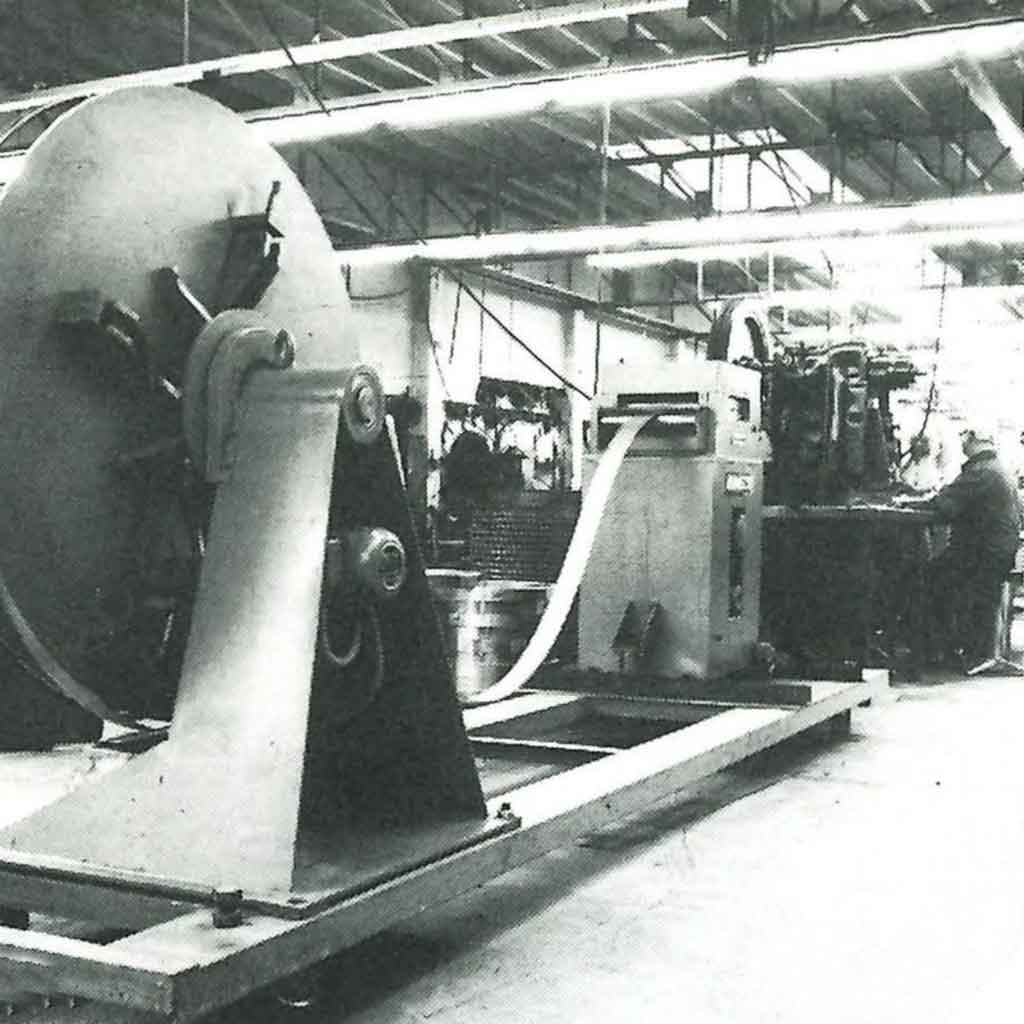
The 1980s
Press brakes
The press braking at Contour began with the introduction of hydraulic Promecam press brakes. These brakes had interchangeable brake tooling, bottom dies, and adjustable back gauges.
The material was still pressed into the bottom die (usually 89 degrees) with great force. The end result was a perfect 90-degree angle. This technique was also called "bottoming."
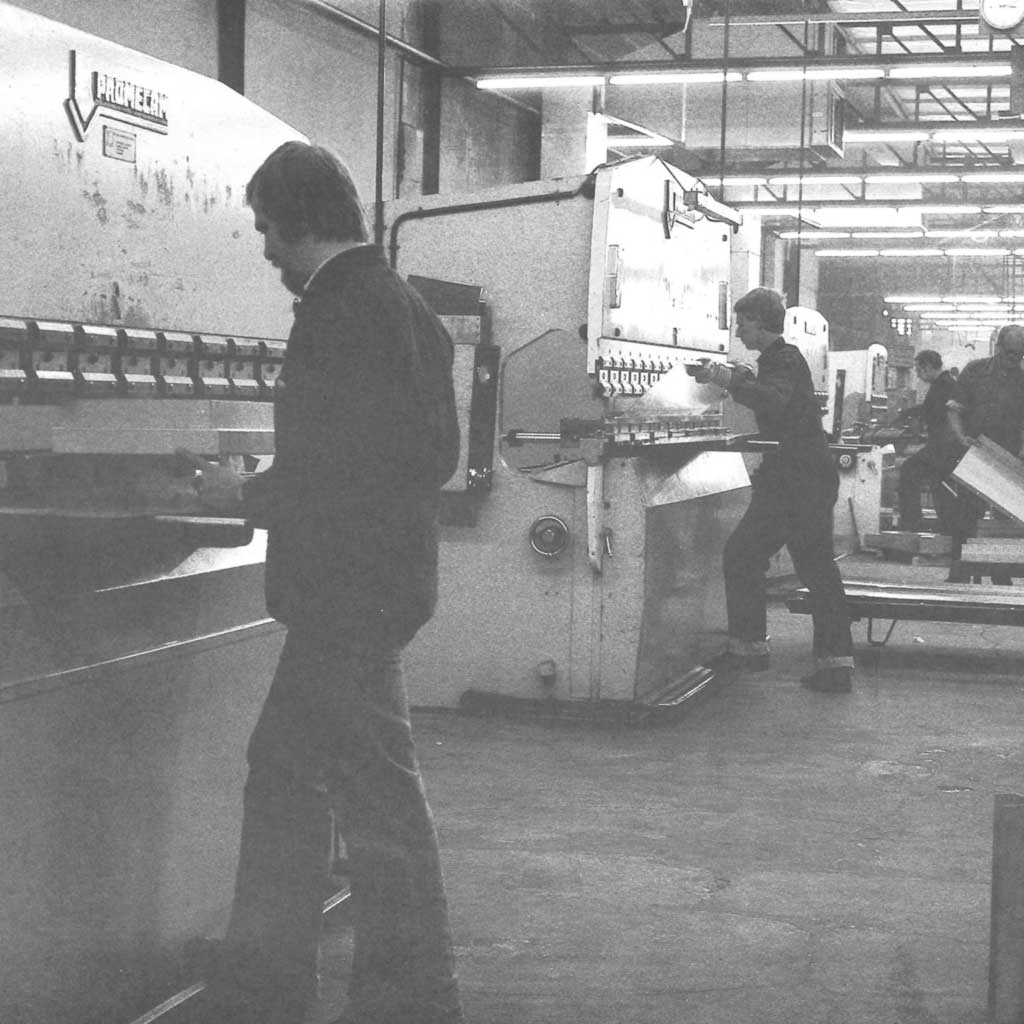
Introduction of CNC punching
The CNC control of sheet metal machines would spark a revolution in the sheet metal industry.
A flat sheet metal part was so far made by "hard tooling" in a single press stroke to punch out a part. One disadvantage was that a separate, costly tool had to be made for each product. The alternative was a series of consecutive manual operations using machines like a guillotine shear, drilling machine, and gas torch.
With the arrival of the Behrens V20 CNC turret punch, many different shapes and contours could now be punched. The machine could run a program that automatically determined the sequence of tooling and coordinates. By making overlapping punch holes, any shape could be punched using standard tooling. "Soft tooling" made its entry.
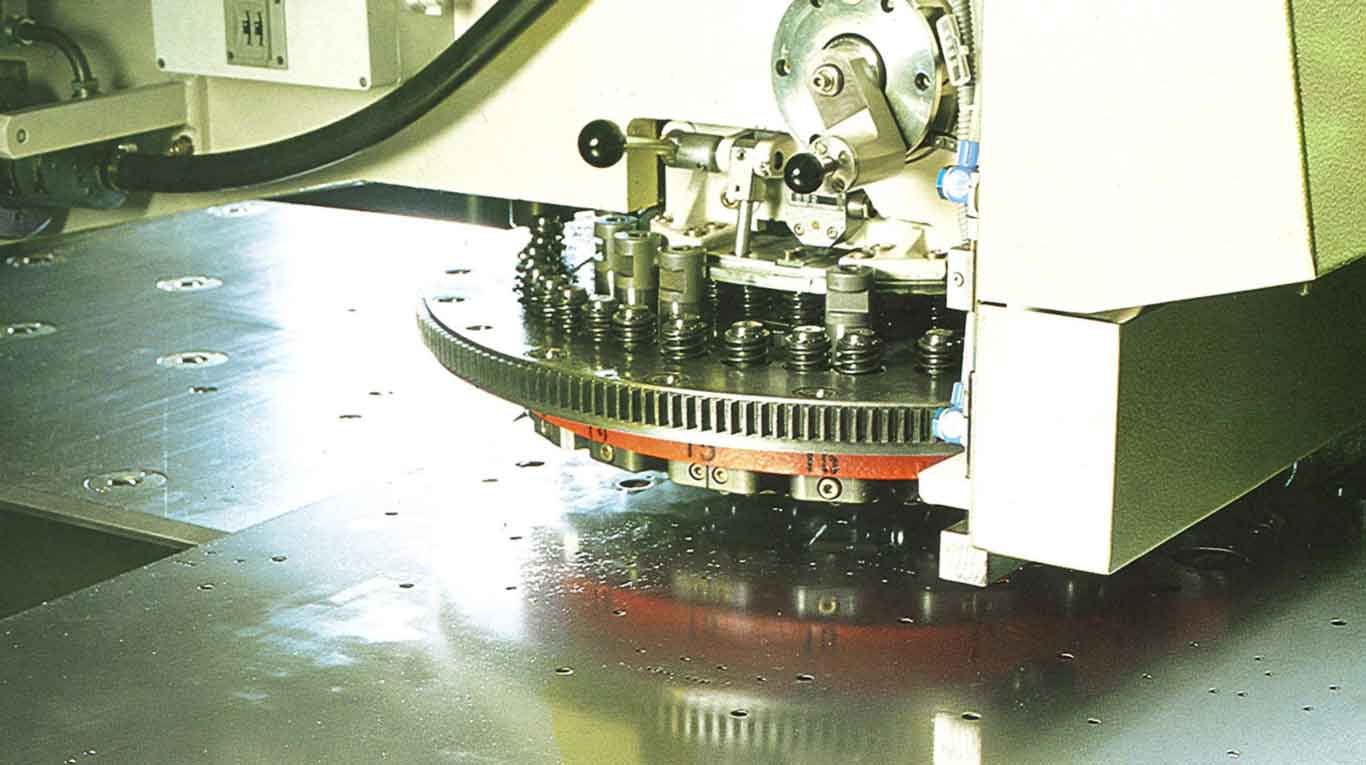
CNC laser cutting
The CNC laser cutting of sheet metal followed soon after the CNC punching and was just as revolutionary a production principle.
In 1981, the Behrens Bel-cut laser cutting machine was purchased. Shown below with a Coherent Everlass 325 laser source from England. This laser source consisted of an oil-cooled tube of about four meters long, around 500W. The system had to warm up properly in the morning before it could cut efficiently. The control was a General Electric from the USA. The cutting table was from Behrens.
Contour (then Sorba Precisieplaatwerk) was the second company worldwide with a CNC laser cutting machine with a Coherent source. Only in California was there a company that had implemented the Coherent laser source earlier.
The Coherent laser source would later be upgraded to a Rofin Sinar 1200W CO2 laser with a roots pump.
The text "ECQ" on the machine stood for Enhanced Cutting Quality.
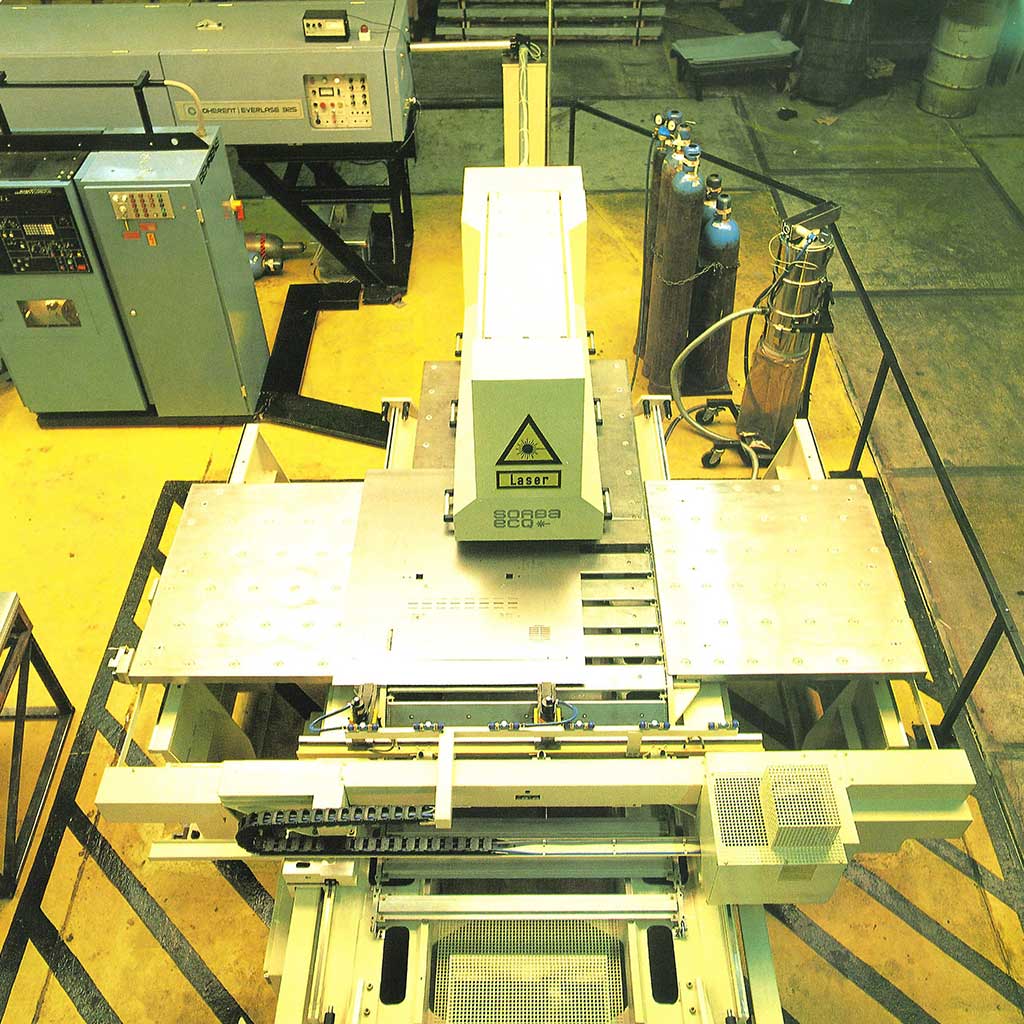
CADCAM
Nowadays a matter of course, in the early 1990s it was pioneering. Creating CNC machine programs based on digital CAD files was in its infancy. Our company was already ahead of the curve. The CADCAM program used here was called Medusa and came from the United States.
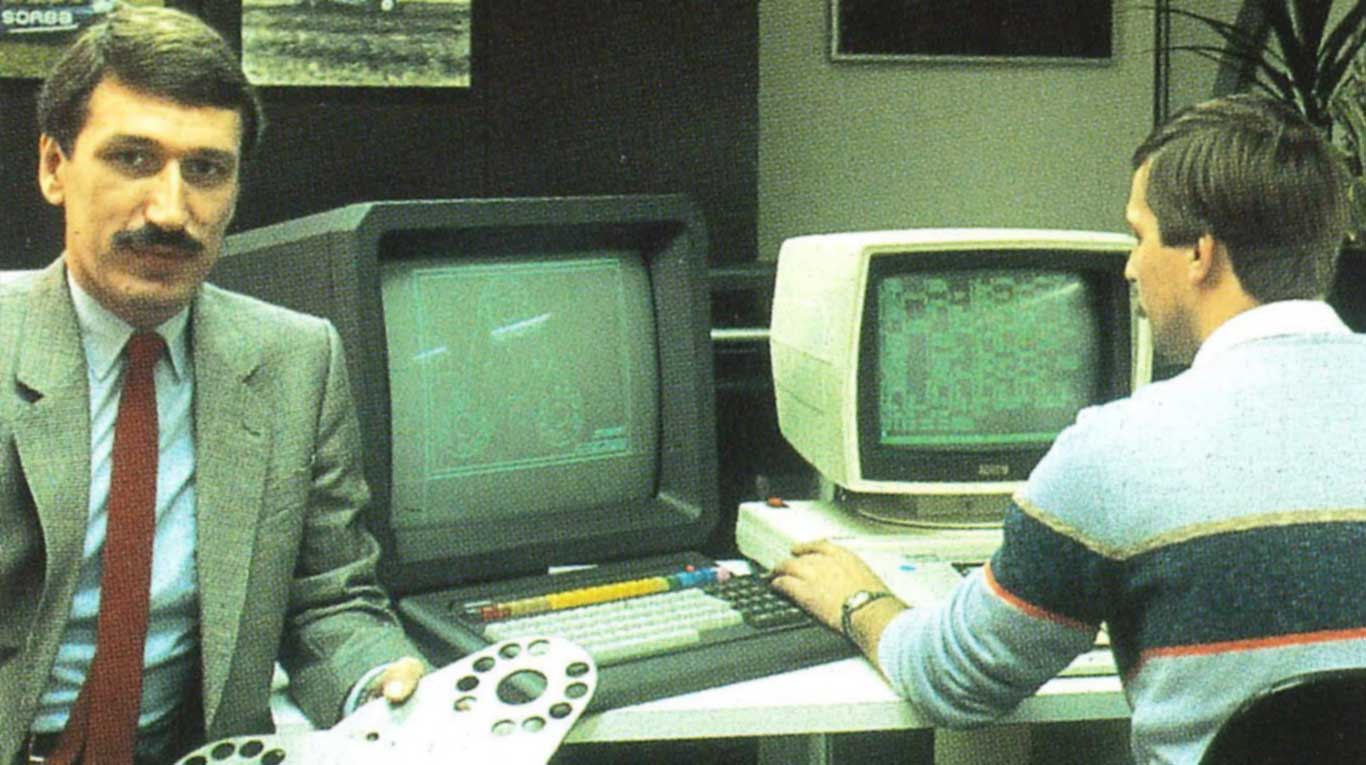
New CNC punching machine
In the 1980s, this CNC Behrens CB 25 punching machine also appeared on the scene.
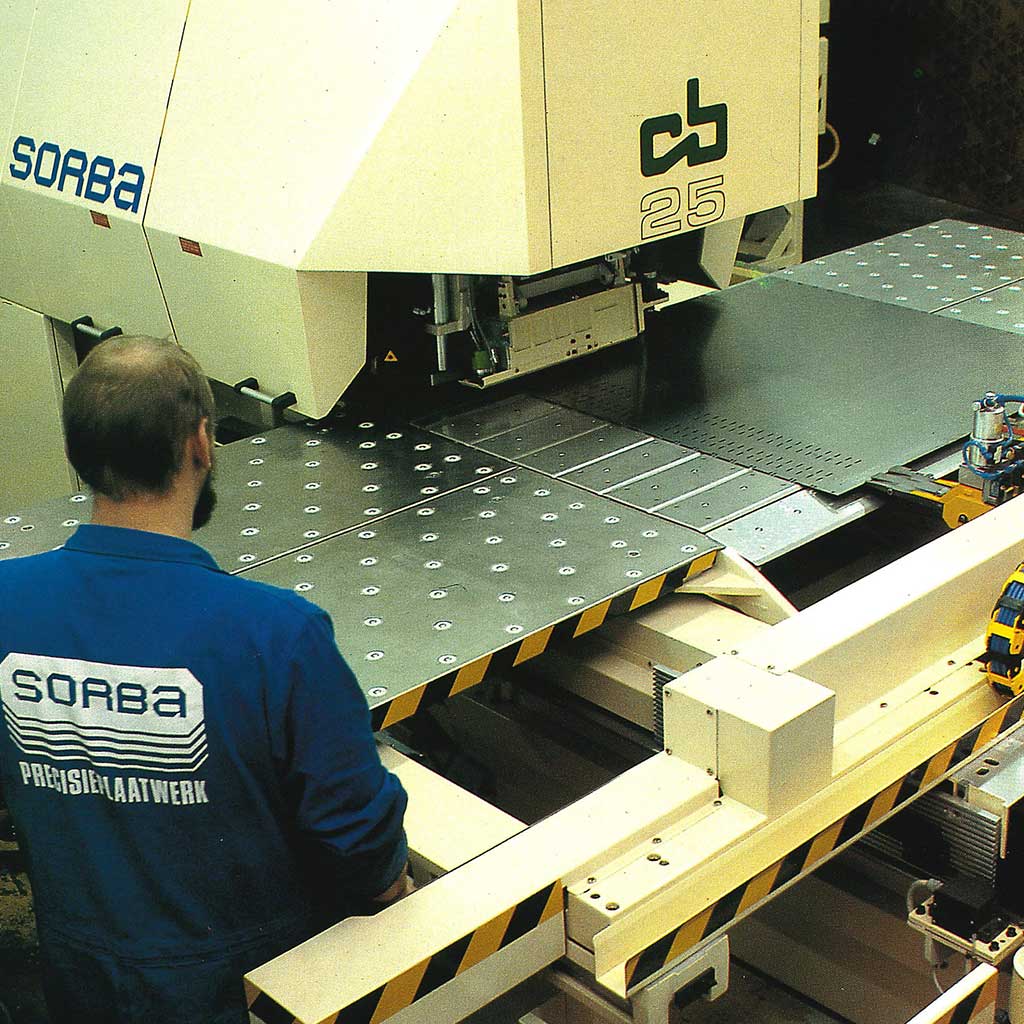
New Combo machine
The revolutionary laser cutting was a success! After the laser source of the Bel-cut was upgraded, the existing Coherent laser source from the Bel-cut was moved to this newly purchased Behrens CB 625 combo machine. This machine could both punch and laser cut, hence the "Combi" name.
The rough design of this machine can still be recognized today in the ultra-modern Trumpf TM7000 punch-laser combo that is now installed in our sheet metal center. This Trumpf machine is still nicknamed "The Combi" at Contour.
In the 1980s, Contour released a brochure explaining the possibilities of CNC punching and laser cutting.
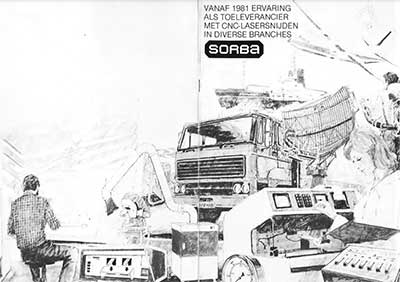
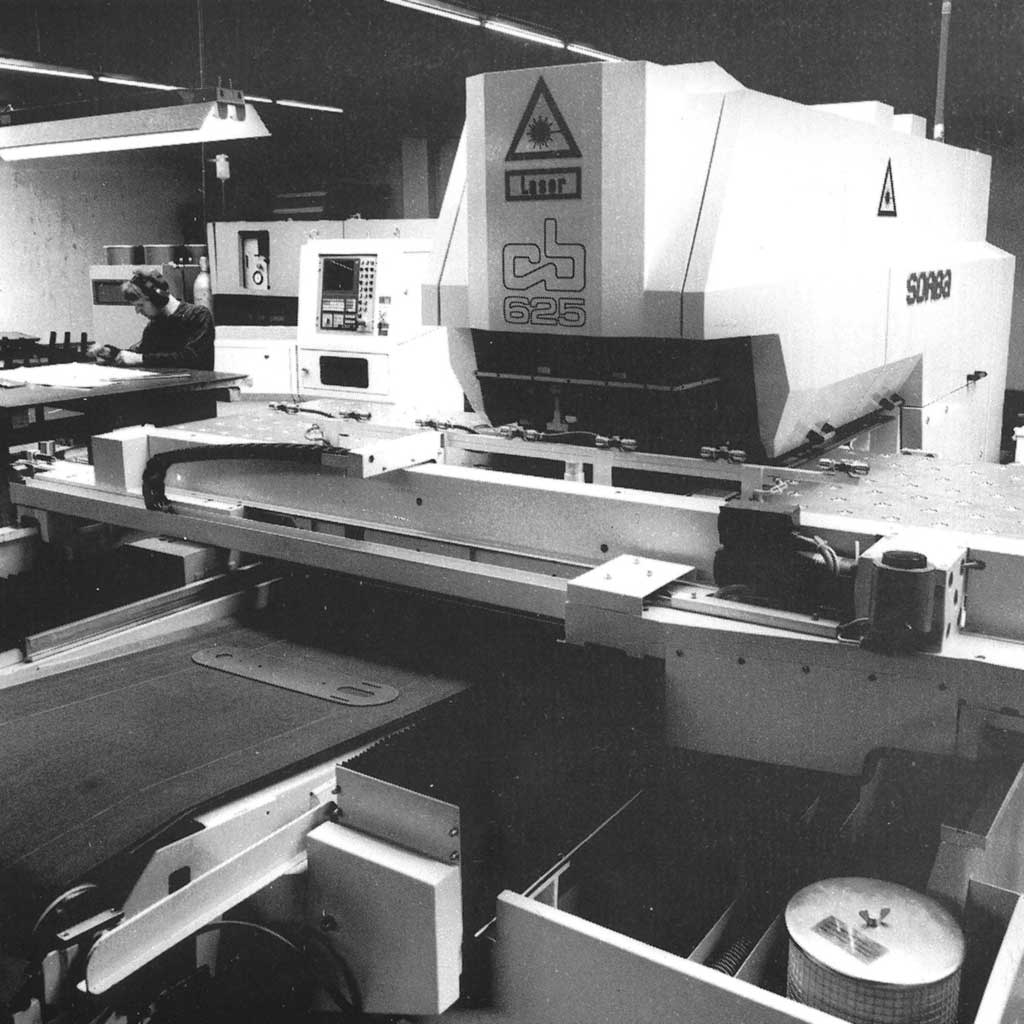
Sheet metal precision
After the decision in '77 to switch the company to precision sheet metal, this article came out in 1981.
In this article from the "metal and plastic" magazine, it is explained why we were enthusiastic about the advent of CNC laser cutting and CNC press braking. It made precision sheet metal possible.
Shearing
Due to growth in processing small-, medium-, and large-format metal sheets, metal shearing was used.
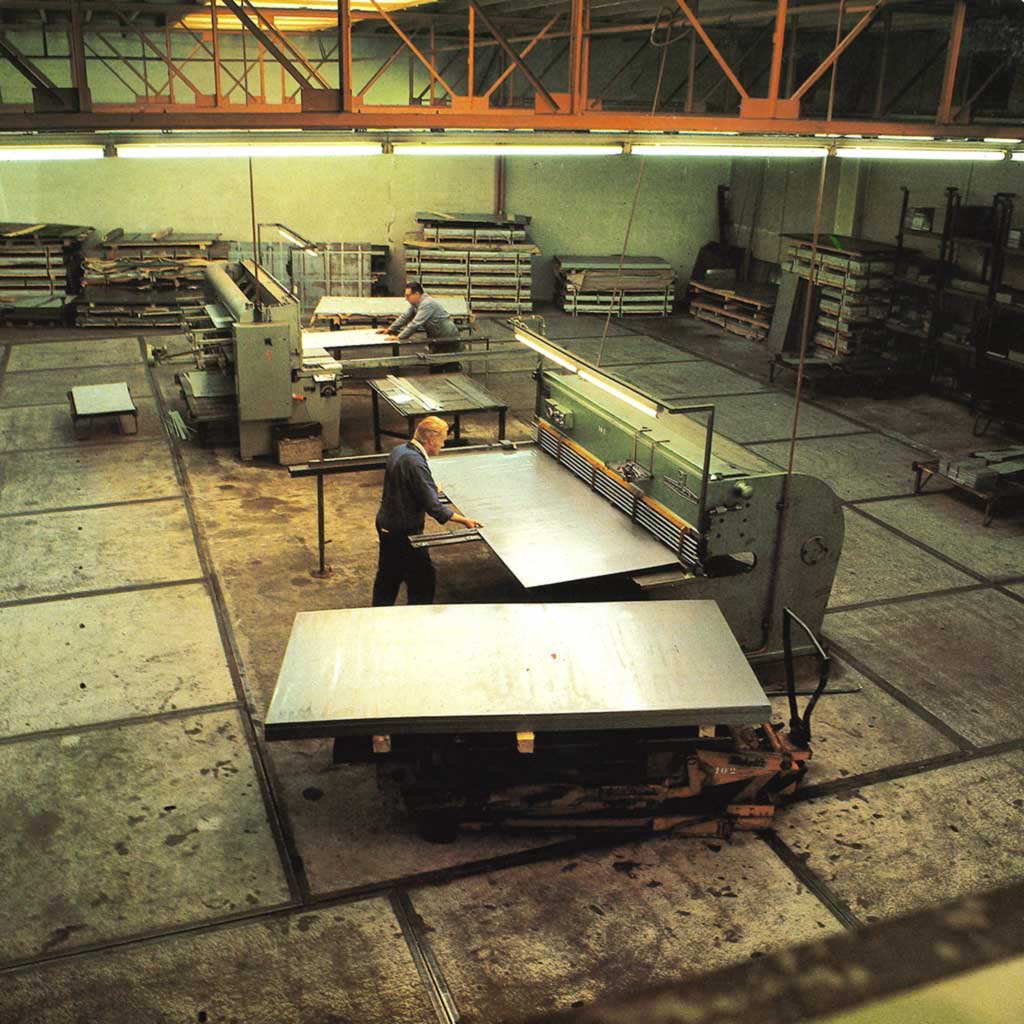
Bigger eccentric presses
The eccentric press was not off the stage in the 1980s yet. With bigger machines, larger sheet metal parts can be produced in one stroke.
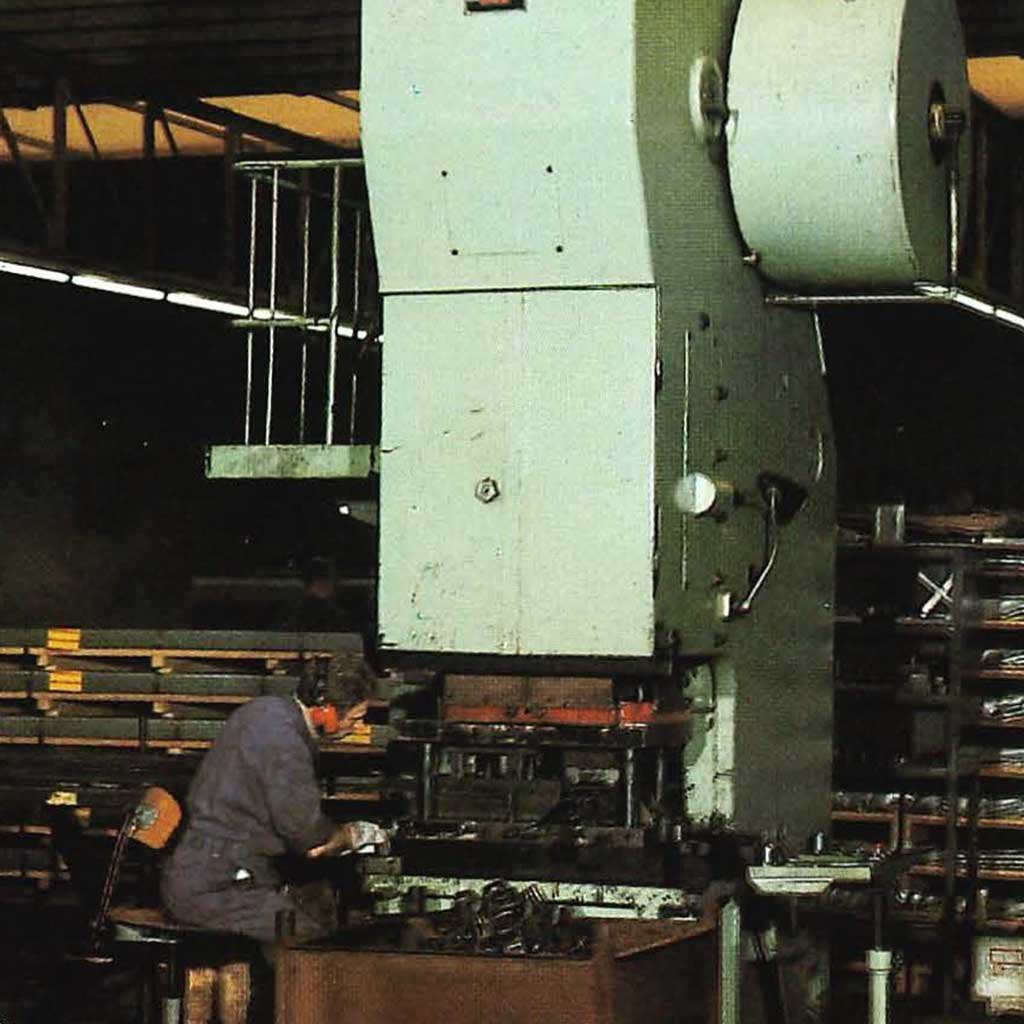
Toolmaking department
Here, a cutting plate for a press tool is being manufactured. The cutting plate is being finished with a sort of automatic file. Smaller press tools were still entirely made by Sorba itself at that time, including hardening of the cutting plates.
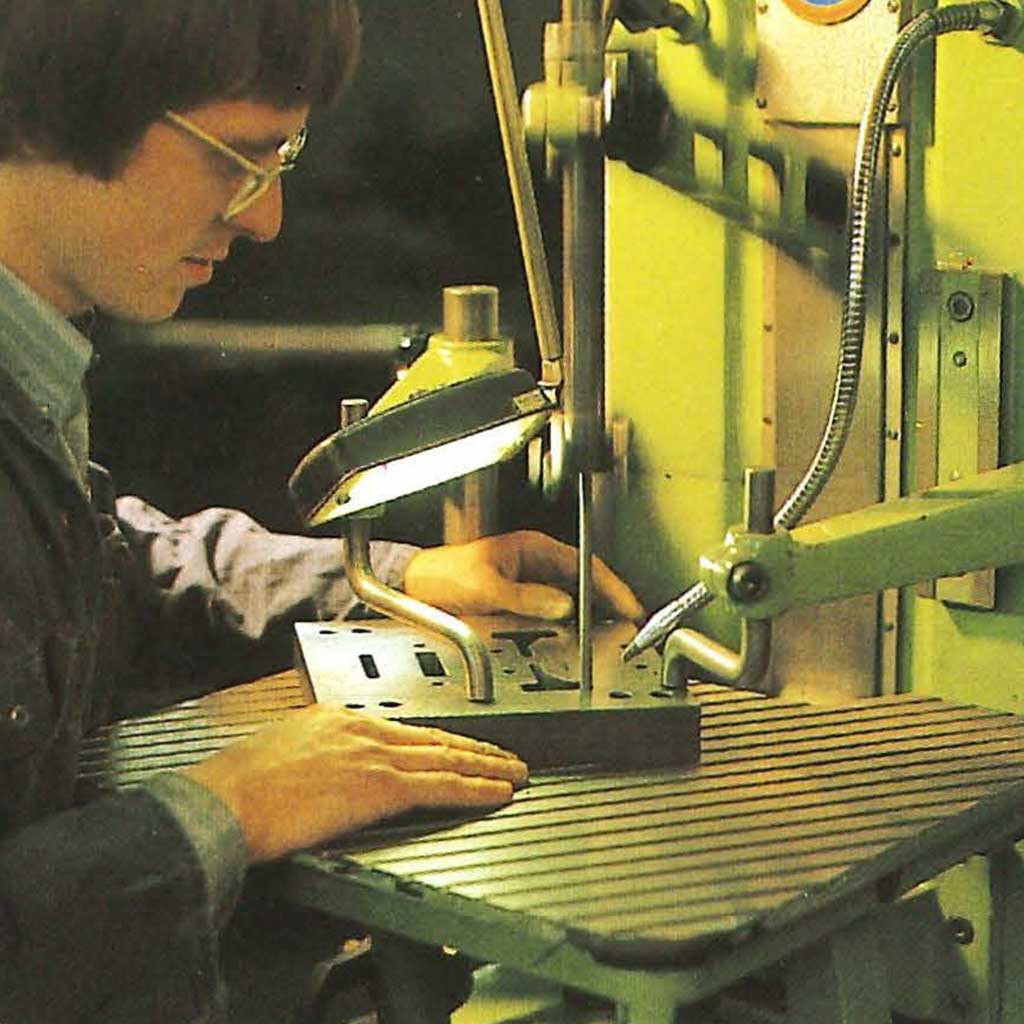
The 1990s
CNC Bending
The CNC-controlled Amada press brake is being introduced!
Through the numerical control, "free bending" or "air bending" becomes possible. With this technique, any desired angle can be produced by precisely defining the penetration depth of the bending tool with high CNC accuracy.
After the material partially springs back, a precise angle remains. This technique places higher demands on the tolerances of both the machine and the sheet thickness.
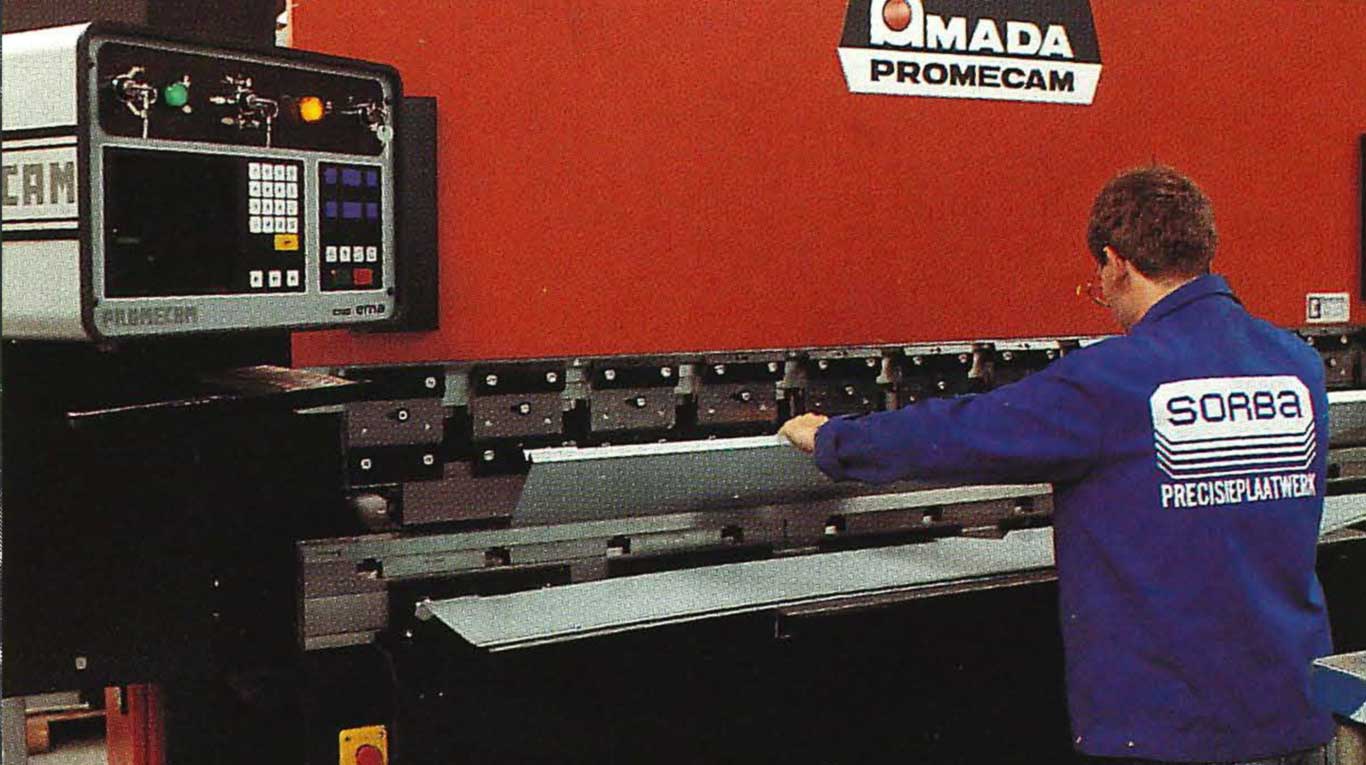
ShSheet metal assembly
The company has increasingly focused on the assembly of sheet metal assemblies.
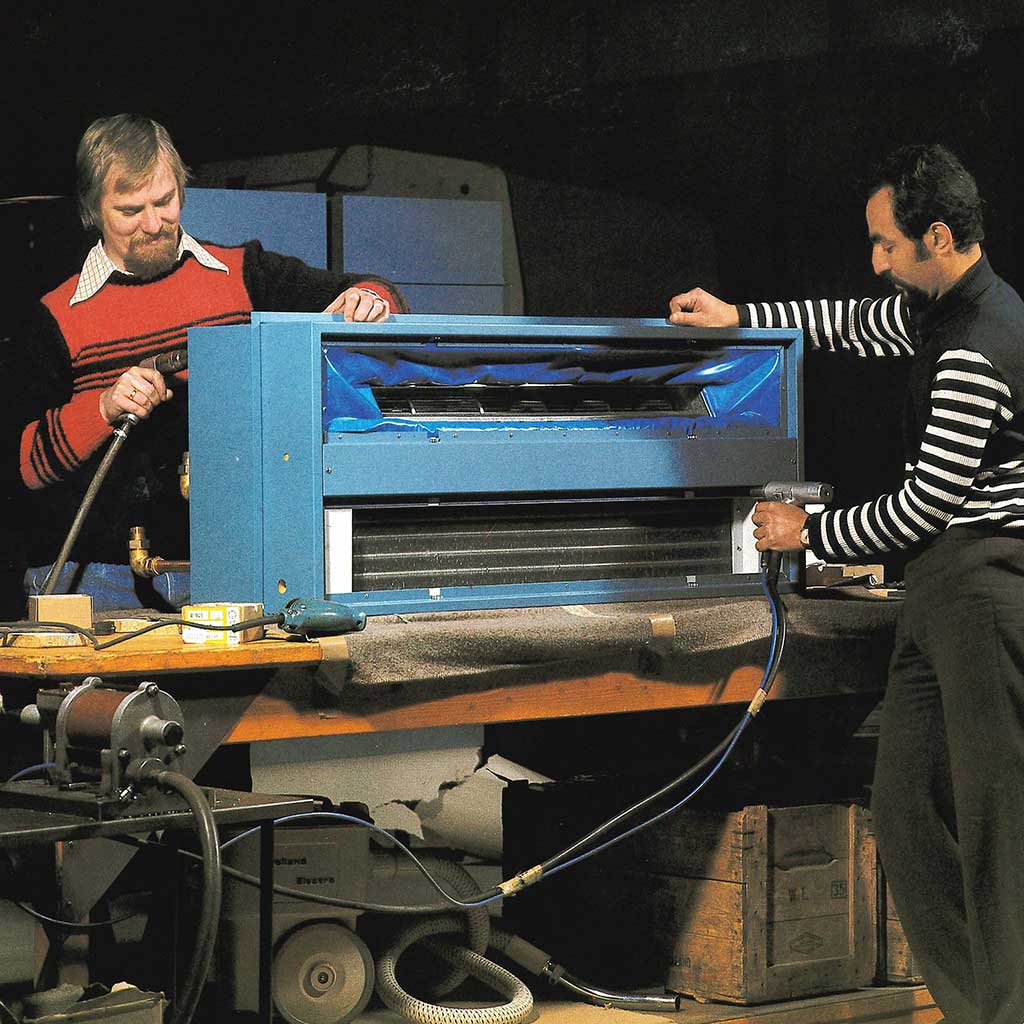
Wet paint stoving
This photo shows a predecessor of the current powder coating installation. Products were given a layer of wet paint. They were then hung in the carts shown and cured in the stoving oven.
The powder coating process was introduced only later for the production of convector enclosures. From this product line, the production of façade cladding emerged. That activity continues to this day at the company that carried on the Sorba brand name. The present-day Sorba specialized in façade cladding, while Sorba precision sheet metal further specialized in sheet metal production. Ultimately, this sheet metal company was renamed Contour Covering Technology BV.
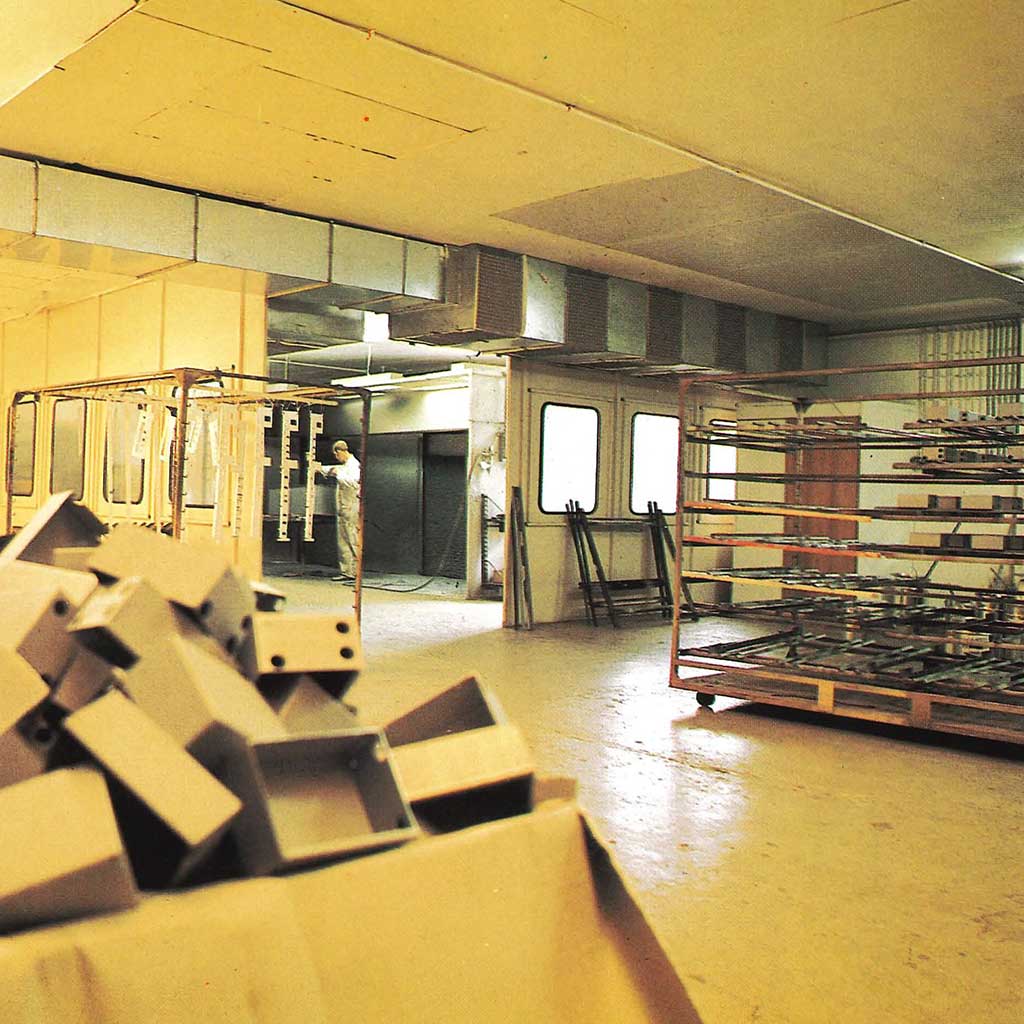
Product: Housings
A few more examples of sheet metal assemblies that Contour supplied to its customers in the 1990s.
With the increasing specialization of companies, the sheet metal work of machines was outsourced more often to specialized suppliers.
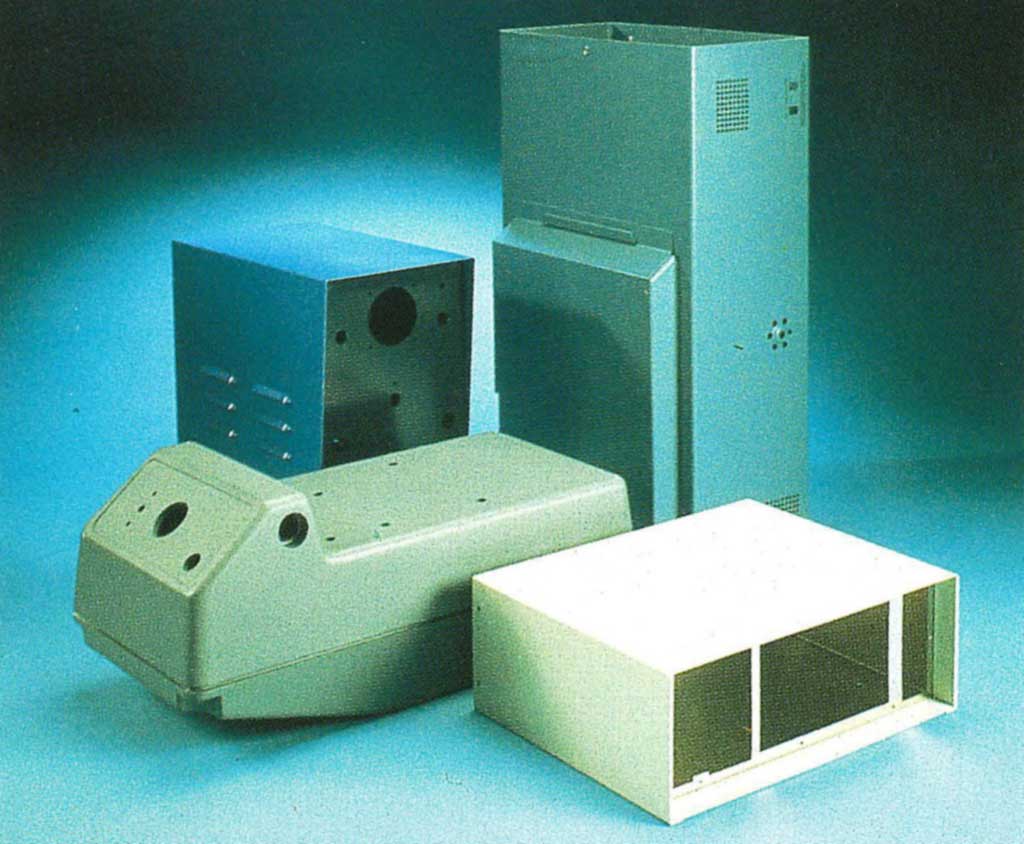
Swing bending
In the 1990s, a swing bending machine was used. It was later replaced by a press brake robot installation.
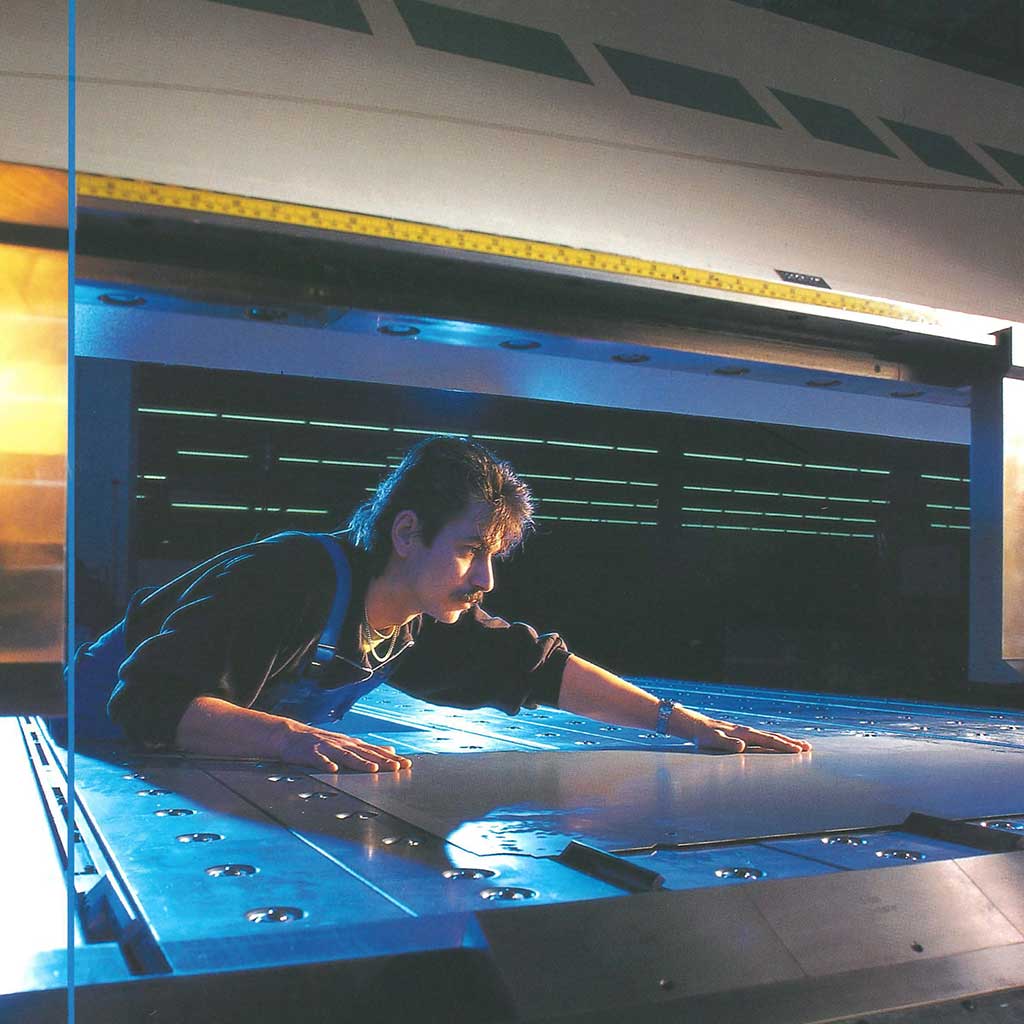
CADCAM Software
When CAD/CAM technology was still in its infancy, it was already being applied at Contour. Under the name "Sorba Engineering," a proprietary CAD/CAM software package for sheet metal was developed, called Origami.
Click here to read an article from 1988 in the German magazine "moderne industrie laser" (pdf).
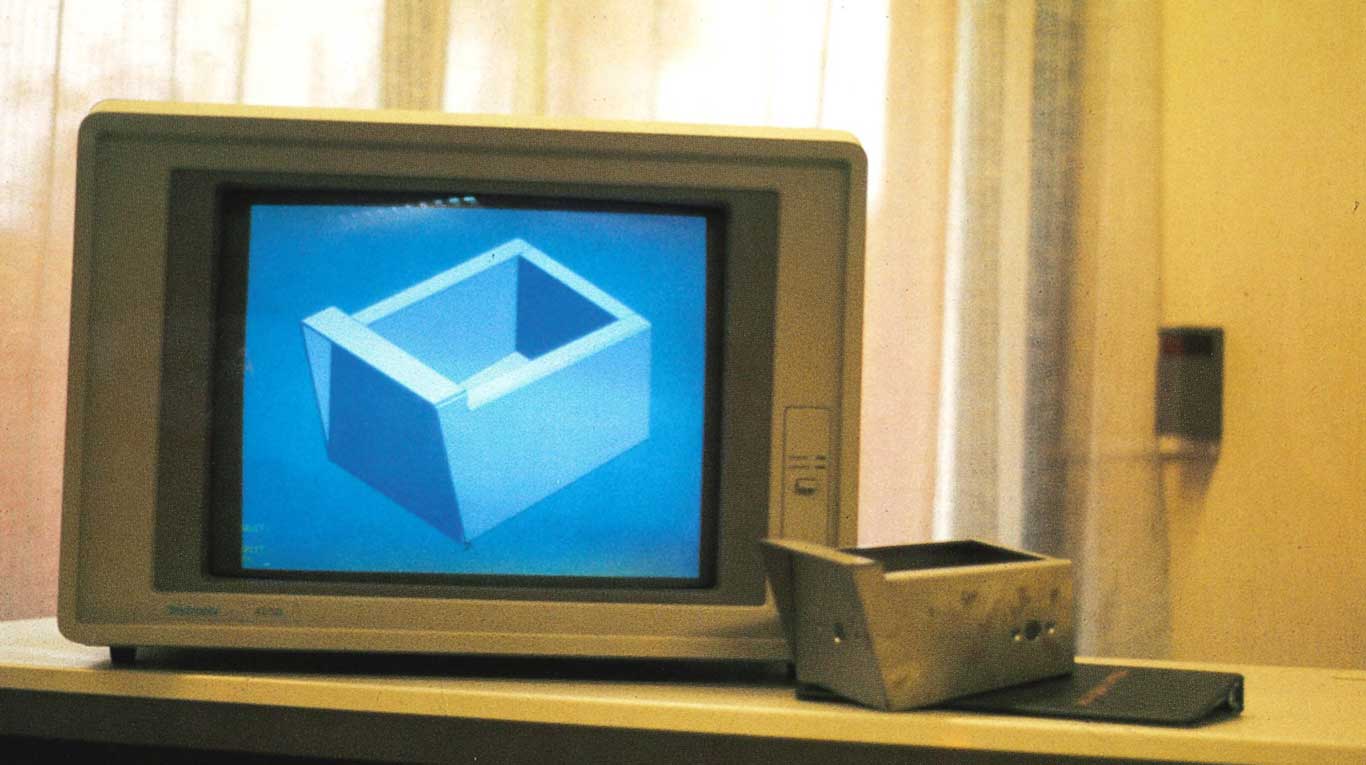
PEMSERT introduction
A process that is still widely used today: "pemserten," meaning the pressing in of press-in fasteners. Nowadays, this is done with modern Haeger machines, but back then it was done with a machine from the U.S.-based PennEngineering.
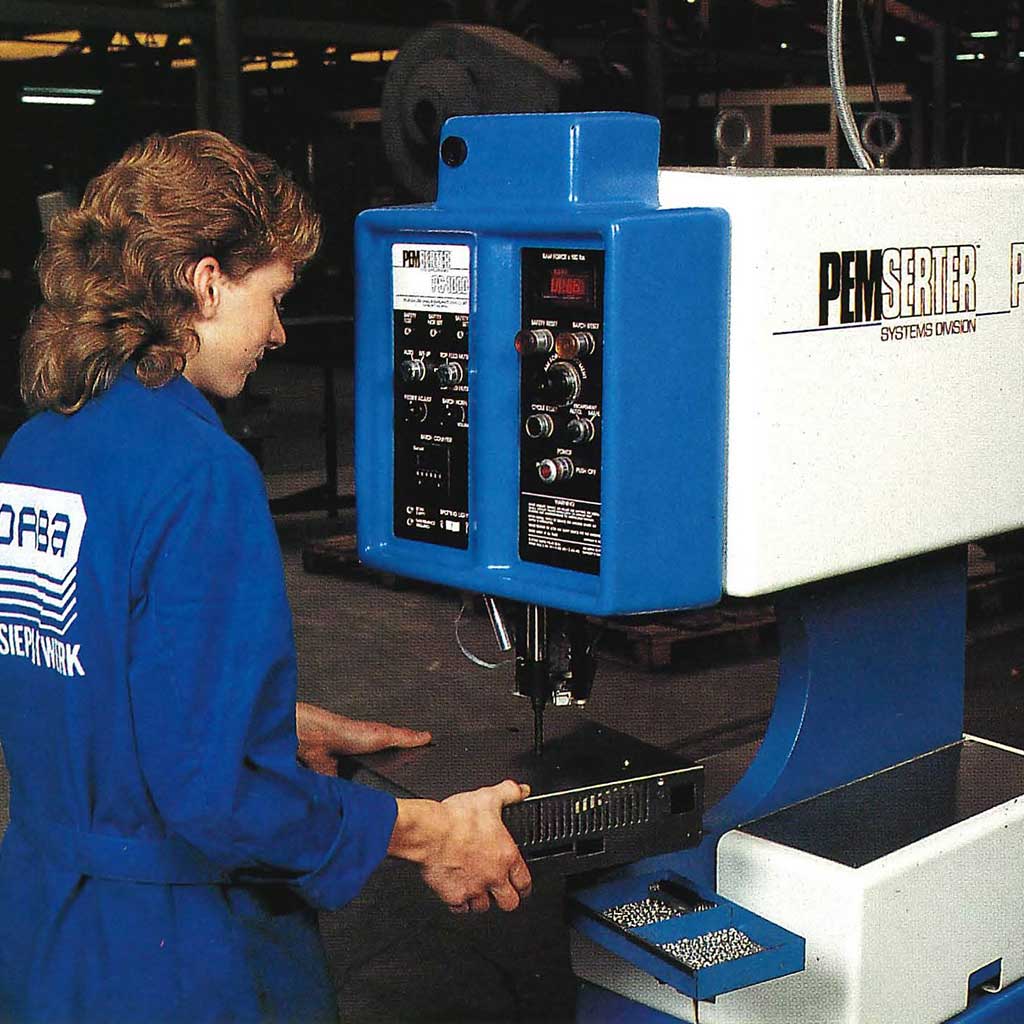
Custom ERP software: PBS
Alongside CAD/CAM, logistics and business operations also received attention. And there, too, it was a matter of pioneering. That's why a proprietary ERP system was designed: PBS, which stood for "production control system."
Today, Contour makes use of the ISAH ERP package.
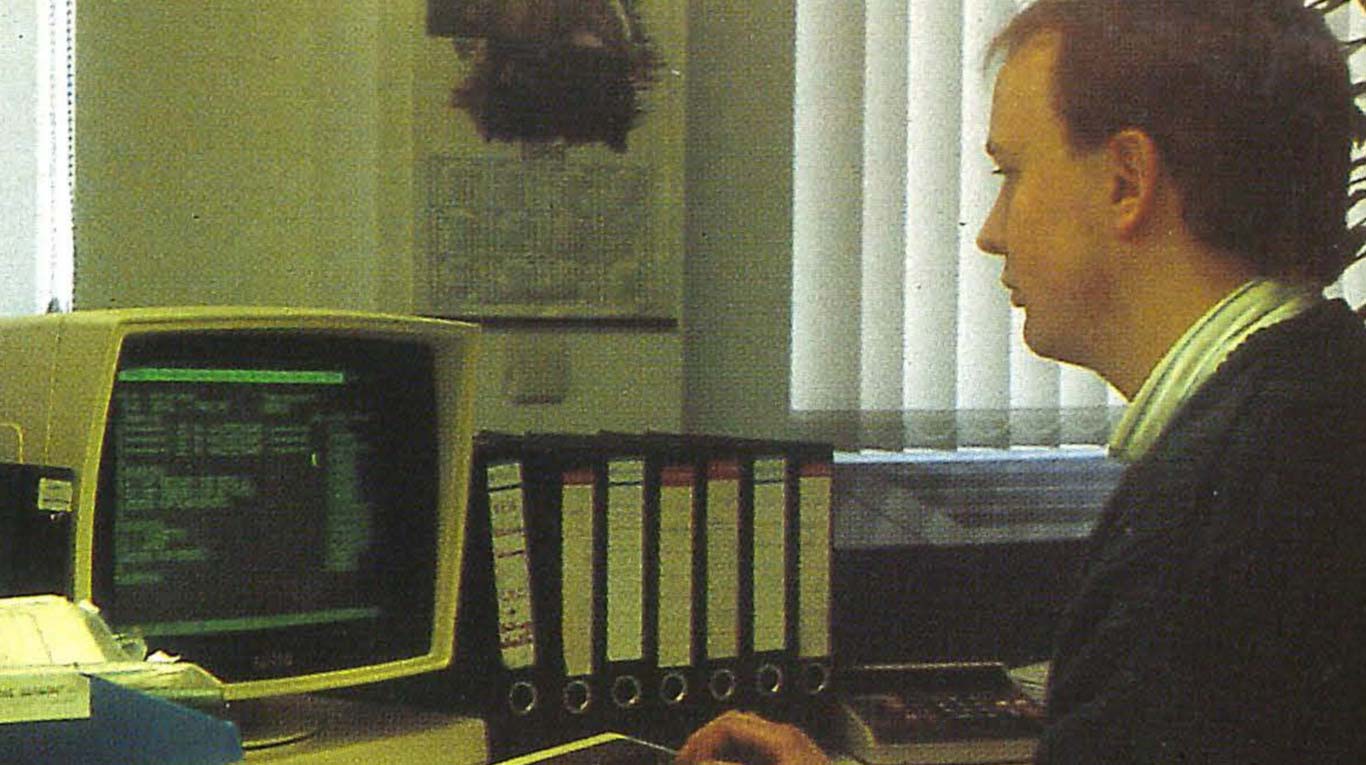
The zero's
2003: Sustainability
In 2003, Contour was featured in the magazine "Winterswijk – Tussen de bedrijven". In this magazine, you can read an article about how Contour, together with the municipality of Winterswijk, had a scan performed to evaluate sustainable entrepreneurship. Among other things, energy and water consumption were charted.
2005: Magazine about Contour
In 2005, an Industrial Insights magazine (pdf) was published about Contour Covering Technology.
This magazine provides a great insight into the 2000s, during which Contour increasingly specialized in serving OEM customers. Various colleagues explain, in this magazine, the changes the company underwent, and several customers also share their perspectives.